Как сделать протектор на колесах модели
Сразу оговорюсь, нарезку протектора, углубляя заводские канавки на непредназначенной для этого резине не советую. Цель моих экспериментов — прорядить имеющийся протектор дорожной резины для превращения ее во внедорожную, сохраняя при этом заводскую глубину канавок.
Итак начнем. Изначально эта мысль у меня возникла, когда износившаяся АТешка на моем внедорожнике перестала меня удовлетворять и своим внешним видом и своей проходимостью на скользкой влажной земле. Я еще тогда подумал: как было бы неплохо здесь и здесь прорезать новые канавки. Позже я узнал, что есть такая штука — регрувер, которая предназначена как раз для этого — нарезки протектора на шинах.
В данной ситуации нарезке подверглись колеса скутера. Причина та же — езжу я на нем чаще по даче и природе, где хорошее сцепление с влажным грунтом или травой важно. Хотел сначала купить новые покрышки Maxxis M6024, но финансы в кризис поют романсы еще больше. Как там медведев сказал: "вы там держитесь, удачи вам и хорошего настроения". Вот и держимся, как можем, мать его.
Так, как такие машинки стоят от 14 тыр до…, что дешевле комплект резины купить, решил поискать что-то по-доступнее. Поиски на али ничего не дали, они тоже стоят там, как… Хотя конструкция у них простая и никак не вложено туда сил и материалов на 15, 20 и 30 тысяч рублей. Думаю высокая цена обусловлена не распространенностью сего девайса.
Стал искать дальше. В интернете многие делают такие машинки сами. Они бывают двух типов: с прямым нагревом, это когда через лезвие проходит ток и оно нагревается, расплавляя резину и косвенным, когда лезвие нагревается от горячего жала устройства, напоминающего паяльника. Многие как раз и делают такие регруверы из паяльников. Прочитав, что лучше использовать паяльники, мощностью от 100 Ватт и до, практически 500, выбрал паяльник на 200 Вт за 879р.
Дальше пошли работы по доработке:
Зажимаем жало в тиски, лучше через прокладку, чтобы мягкую медь не помять и молотком загибаем. Гнется легко. Под конец я еще добавочно погрел в месте сгиба газовой горелкой, чтоб наверняка не порвать в месте сгиба.
Потом замеряем ширину канавки, которую хотим нарезать. В моем случае это 10мм, чтобы не сильно отличалась от имеющихся канавок.
Потом замеряем, в каком месте у жала будет эта толщина и размечает керном:
Потом аккуратно под прямым углом отпиливаем кусок болгарочкой или ножевкой.
Получилось вот, что:
Далее замеряем глубину нарезаемого протектора:
и из отрезанного кусочка, делаем шаблон, с толщиной протектора. :
В моем случае это получилось 4.5мм*9мм. Этот шаблон нужен будет при изготовлении лезвия правильной формы и с правильным вылетом.
Напильником ровняем и вот, что получаем:
Следующий шаг — это обтачивание жала на точиле так, чтобы по бокам были параллельные друг другу плоскости. Это не обязательный шаг, но желательный, чтобы при сверлении у нас получились строго перпендикулярные отверстия:
Следующий шаг — сверление отверстий. В качестве лезвия я взял лезвие от канцелярского ножа на 9мм, прислонил его к стороне жала и нацарапал две полоски, обозначил место, где это жало будет лежать. Потом отступив пару миллиметров от этих полосок в стороны, накернил и просверлил 3 сквозные отверстия на 3мм под 3мм винтики, купленные заранее с гайками и шайбами. Лучше винтики с гаечками купить закаленные (черненькие). При сверлении учтите, что медь — мягкий металл и сверлить его, как ни странно сложно, так, как можно легко сломать сверло завязнувшее в материале и потом его оттуда хрен достанешь.
И вот, после сверления, которое я не сфоткал, прикручивается лезвие одной стороной к жалу, жало зажимается в тисках и лезвие нагревается газовой горелкой до красна, подкладывается наш маленький шаблон и пассатижами загибается до противоположной стороны жала.
Потом, когда всё остынет, винты откручиваются и прижимается вторая сторона лезвия:
Совсем недавно в нашей рубрике мы говорили о расшивке и применении пилок для её восстановления.
Есть у этого инструмента еще одно применение. С его помощью можно восстановить или нарезать простой протектор на покрышках.
Зачастую пластиковые колеса на моделях самолетов и другой техники выполняются из двух половинок. Обусловлено это технологическими причинами, но моделистам от этого не легче. Ведь при зачистке стыка половинок колеса стирается протектор и смотрится такое колесо грустно. Можно конечно найти замену в виде смоляной или резиновой покрышки, но это лишние траты, да и не всегда их легко достать или просто найти.
В таком случае протектор можно восстановить, благо на самолетах он зачастую весьма простой и представляет из себя поперечную насечку или "сеточку".
Просто берем пилку и аккуратно прорезаем пропавшие линии протектора, кладя лезвие пилки в канавку сохранившегося протектора и ведя пропил "на себя". В случае если протектор надо нарезать с нуля - его стоит сначала разметить на детали, тем же карандашом.
Если протектор на колесе довольно глубокий - его стоит сначала наметить пилкой, и потом проточить треугольным надфилем.
И не забываем пролить нарезанный протектор супер-текучим клеем. Это уберет из нарезанных линий пластиковую пыль и несколько сгладит их грани, придав больше сходства с резиной.
Аналогичным образом можно восстанавливать и простой продольный протектор, правда тут понадобится большая аккуратность и разметка ровной линии.
- Новые материалы
- Популярные
Сегодня мы хотим поделиться с вами моделью «Звездного Разрушителя» от Звезды и рассказать о том, как эта модель строилась.
В свете текущего переезда нашего магазина нам в голову пришла отличная идея для статьи
В рамках сегодняшней модельной рубрики мы продолжим рассказ о сборке моделей бронетехники.
В прошлых статьях раз речь зашла о применении шпаклевки для весьма узкой и специфичной цели
Приобрели на днях вот такой вот симпатичный грузовичок ЗИЛ-5301 "Бычок". К сожалению с ним в комплекте не оказалось запасного колеса, которое должно было крепиться сзади к раме. Не долго думая, решил по быстрому слепить формочку и отлить недостающее колесо из эпоксидной смолы. Благо, есть с чего снимать слепок и делать копию, к тому же ещё не успел выбросить остатки желатина от всех этих форм. Вот только пришлось сначала немного помучиться, чтобы снять колёса с передней оси грузовичка. После чего, форма для копии колеса, была сделана буквально за несколько минут, куда дольше сохла сама эпоксидка в этой форме.
Собственно вот здесь должна была крепиться запаска этого ЗИЛ-ка (фото ниже). Сейчас же в этом месте пока гуляет ветер :-)
Из полосы пластика сворачиваем кольцо (опалубку) чуть больше самого колеса. Старайтесь не делать очень широкую форму, так как в последствии при разрезании формы, сложно будет искать середину шины, ибо толстая масса желатина плохо просвечивается. Идеальный вариант, это когда толщина стенок желатина вокруг детали, лежит в пределах 5-10 мм. Но это опять таки всё зависит от размеров самой детали, в моём случае, это колесо диаметром около 15 мм.
Разогреваем желатин и заполняем на треть или половину, нашу пластиковую опалубку. Затем даём остыть этой подложке, Это нужно для того, чтобы при погружении колеса в горячую массу, оно не опустилось на дно, а осталось в середине нашего резинового цилиндра.
Окунаем колесо в горячую массу и хорошенько промазываем кисточкой все щели и вогнутости на колёсном диске. Не забываем про рисунок протектора на шине. В общем, чем тщательней обмажете, тем более качественнее будет отпечаток, и соответственно меньше будет в последствии пузырей на копии колеса. Если погружаемая деталь довольно массивная, то после погружения в массу, даём ей какое то время, чтобы она прогрелась до температуры желатина.
После того как колесо обмазали и избавились от всех воздушных пузырей на нём. Не щёлкая долго варежкой, цепляем его пинцетом и переносим на заранее подготовленную желатиновую подушку. При этом надо постараться зачерпнуть самим колесом побольше желатина, чтобы как бы приклеить его к основанию. К тому же меньше будет шансов, опять нахватать пузырей при переносе колеса в опалубку. После чего выравниваем колесо, чтобы оно лежало горизонтально и посередине. При необходимости, доливаем ещё желатина, заполняя тем самым опалубку до самых краёв.
После остывания массы, можно смело разматывать пластик с этого резинового цилиндра.
Делаем надрез и извлекаем резиновый оригинал колеса. Надо постараться попасть в торец шины, вот именно по этой причине, желательно делать стенки формы не очень толстыми. Так как в этом случае, положение колеса хорошо прощупывается пальцами, а иногда его даже видно на просвет. Надрез делаем не очень длинный, где то на треть меньше диаметра самого колеса. Через большой надрез, неудобно будет заполнять форму, ибо эпоксидка будет вытекать.
Не спеша заполняем форму смолой, чтобы воздух успевал выходить. Зубочисткой или иной палочкой, распределяем смолу по всем углам и пазам формы, чтобы избавиться от воздушных пузырей, а в последствии и раковин на колесе. Нежно схлопываем половинки, при необходимости, подпираем чем нибудь, чтобы створки не раскрывались.
В моём случае, одна из половинок разрезанной формы, просела чуть ниже и никак не хотела выравниваться, в результате шов был как ступенька. Поэтому выждав когда смола станет менее текучей (густой), положил форму на бок и сверху слегка придавил грузом. После этого, ступенька исчезла и шов выровнялся заподлицо. Так же не следует сдавливать форму очень сильно ибо может произойти схлопывание половинок в сердцевине и в результате на выходе мы получим отдельно шину, и отдельно фрагмент колёсного диска.
Иногда удаётся извлечь эпоксидные отливки без разрезания формы, например как этот череп-брелок. Но здесь этот способ не прокатил, отливка прилипла намертво, пришлось разрезать и разрывать форму.
На фото ниже, фрагменты разорванного желатина, который остался в щелях колёсного диска. Но все эти остатки резины, легко смываются горячей водой из под крана, ибо желатин прекрасно плавится и растворяется в воде. При этом даже не нужно пытаться вычищать остатки всякими зубочистками. Только перед этим, старайтесь выдержать отливку из эпоксидки не менее суток, на воздухе или в самой форме. Так как не полностью схватившаяся эпоксидная смола, начинает покрываться белёсым налётом в горячей воде. Сам я опыты не ставил, но возможно эта водяная баня на полусырой отливке, скажется в последствии на детализации самой детали.
Собственно, наше колесо собственной персоной, после водных процедур :-)
На просвет хорошо видно насколько тонка перемычка между лицевой и задней частями колеса. Именно по этой причине, не следует сильно сдавливать форму после заполнения её смолой, так как две половинки формы могли соединиться, и эта перегородка просто исчезла бы.
Чуть ниже на фотке, результат других моих экспериментов. Здесь к сожалению не полная 3D-копия колеса, но зато оно имеет более мощную осевую часть. К тому же, такая полуоткрытая форма легче в изготовлении, даже ось снимать не обязательно. Правда остаётся ещё решить проблему с центровкой и высверливания отверстия для металлической оси, в центре колеса.
Здесь отметил где прошёл шов от половинок формы. Хорошо видно что половинки формы соединились практически идеально. Если бы я не положил форму горизонтально, то скорее всего здесь была бы ступенька.
Тыльная сторона диска. Если на оригинале колеса, перед погружением его в желатин, залепить эти ямы хотя бы на половину, гипсом, картонкой или ещё чем. То можно будет не опасаться схлопывания половинок формы, ибо зазор станет больше, ну а диск соответственно толще.
Возле своего собрата, с которого собственно и отливалась эта копия.
Немножко видео с установленным на своё место, запасным колесом.
В общем результат клонирования мне очень понравился, есть конечно некоторые косяки в виде мелких раковин и пузырей, но они настолько ничтожны, что их даже не замечаешь (если не вглядываться). Надписи читаются, протектор угадывается, а больше вроде ничего и не нужно, тем более это колесо будет смотреть в пол :-) По крайней мере, теперь всегда можно отлить копию какого либо колеса вместе с колёсным диском, для какой нибудь из этих машинок в масштабе 1:43. Некоторые покрышки которых, имеют неприятное свойство плавить пластиковые диски на этих же машинках. Но так как этот вариант копирования несколько муторный, то им лучше пользоваться когда диск на какой либо машине полностью разъело. Поэтому не допускайте полного плавления диска, то есть чаще осматривайте свою коллекцию моделей, чтобы успеть принять меры. Кстати, ранее я уже выкладывал небольшую темку про отливку покрышек для машинок, там способ несколько проще этого, но зато сразу отливается куча покрышек, которые затем шлифуются и устанавливаются вместо резиновых.
Написать сообщение автору
Автор: Nikolay Golovin - - - - - - - -
03.09.2015
В некоторых случаях практически «лысая» авторезина может еще послужить. Для этого на ее поверхности нарезается новый протекторный слой. Нарезку протектора шин можно выполнить своими руками, используя специальные инструменты, приобретенные в автомагазине либо изготовленные в домашних условиях.
Какие автошины можно восстановить?
Нарезка протектора шин осуществляется на покрышках грузовых автомобилей. Производителями такой авторезины для грузовиков предусмотрена возможность выполнения нарезки: автошины изготавливаются с дополнительным слоем резины и усиленным каркасом. У легковой авторезины дополнительного слоя нет, поэтому углубить высоту протекторного слоя не удастся.
Нарезку канавок можно выполнять на автопокрышках, имеющих маркировку regroovable, нанесенную на боковой поверхности изделия. При этом необходимо соблюдать следующие условия:
- Углублять можно протектор до допустимой производителем автошины глубины. Иначе есть возможность повреждения кордового слоя. Узнать допустимую высоту восстановления канавок можно по индикатору нарезки, присутствующему на поверхности покрышки. Индикатор высоты нарезки протектора имеет вид небольшого углубления, находящегося в основании протекторного слоя. Благодаря указанному индикатору можно определить высоту восстановления канавок.
- Нарезка автопокрышек выполняется при остаточном протекторном слое 3 мм — это позволяет видеть канавки протектора и восстановить их глубину до необходимой нормы.
- Восстанавливают канавки при помощи специального устройства, называемого регрувером.
Применяя нарезку можно продлить ресурс автошин на 25% от рекомендованного пробега производителем резины. Это позволяет сэкономить деньги на приобретение новых автошин.
Среди автолюбителей есть мнение, что нет необходимости нарезать протекторный слой, можно использовать автошины до полного их износа. Такая позиция ошибочна, ведь с практической стороны, при истирании резины до индикатора износа автопокрышка становится похожей на слик. Использование сликов для грузового транспорта может привести к аквапланированию при попадании воды в пятно контакта колеса с дорожным покрытием. Если учитывать нагрузки, которые действуют на колеса грузовиков, то при возникновении эффекта аквапланирования машина становится просто неуправляемой. Нарезка шин позволяет увеличить протекторный слой с глубиной 3 мм до протектора с высотой слоя от 6 до 9 мм. Это значительно улучшает отвод воды при соприкосновении колеса с мокрым покрытием дороги и гарантирует большую безопасность при передвижении транспортного средства. Преимущества нарезки авторезины:
- продление ресурса автопокрышек;
- увеличение тяговых свойств автомобиля;
- снижение сопротивления качению;
- экономия топлива;
- увеличение безопасности передвижения особенно по мокрому либо скользкому дорожному покрытию.
Рекомендуем посмотреть видео о нарезке протектора шин самодельным регрувером:
Указанная услуга по восстановлению протекторного слоя очень распространена для таких категорий транспорта:
- Грузовые автомобили. Стоимость автошин грузовиков существенная, поэтому многие владельцы указанного вида транспорта прибегают к услуге восстановления протекторного слоя. В большинстве случаев нарезают резину с маркировкой R22,5.
- Внедорожники, болотоходы. Автолюбители, предпочитающие транспорт, обеспечивающий проходимость в труднодоступных рельефах часто проводят соревнования между собой. Чтобы добиться первенства в гонках по непролазной грязи они изменяют рисунок протекторного слоя и его глубину для обеспечения большего сцепления колес с покрытием дороги, частично удаляют ламели на заводских шинах. Такие действия обеспечивают проходимость машины по непролазной грязи и сложным рельефам, уменьшаются шансы застревания автомобиля. Многие автомастерские предоставляют услуги: создание специальных шин из грязевых и болотоходных заводских покрышек, по индивидуальному чертежу заказчика. Допускается расширение канавок, изменение их формы и глубины.
- Погрузчики и специальная техника. Для указанного вида транспорта применяются цельнолитые автопокрышки, имеющие большую глубину протектора. Нарезка цельнолитых шин дает возможность сэкономить расход горючего, обеспечивает больший эксплуатационный период покрышек.
Изготовление самодельных регруверов
Нарезать протектор шин позволяет специальное устройство — регрувер. Он представляет собой приспособление, прорезающее канавки протектора раскаленным лезвием.
Регруверы разделяют таким образом:
- Приборы с прямым нагревом. В них электрический ток идет непосредственно через лезвие, нагревая его. Изготовить такое устройство своими руками сложно: необходим преобразователь для сварки, который есть не у каждого автолюбителя.
- Устройства с непрямым нагревом. Для такого инструмента ток проходит не через лезвие, а через нагревающийся элемент, к примеру, жало выжигателя либо паяльника, к которому закрепляется нож.
Как можно сделать самодельный регрувер? Вариантов изготовления указанного устройства очень много, мы укажем самые распространенные:
Самодельный регрувер, основой которого служит паяльник
Из паяльника с мощностью от 0,3 до 0,5 кВт. Изготавливается прибор, позволяющий нарезать авторезину, следующим образом:
- из бытового паяльника извлекается нагревающий элемент;
- если наконечник слишком острый или скошенный под определенным углом, то его выравнивают напильником;
- в выровненном наконечнике сверлится отверстие для закрепления U-образного ножа;
- нож крепится при помощи болта;
- после установки ножа на прибор, выполняется обратная сборка паяльника.
Самодельный прибор из выжигателя, имеющего мощность не меньше 200 Вт. Процесс изготовления регрувера следующий:
- Из выжигателя извлекается нагревательный элемент.
- К элементу нагрева крепится двустороннее бритвенное лезвие.
- Из пера выжигателя извлекаются провода.
- Берутся две пластины из меди с сечением 1х1 см и длиной 3 см, в них просверливаются сквозные отверстия, их количество шесть штук. В каждой пластине должно быть три отверстия. По три отверстия должно размещается на одной грани пластины. Первая пара отверстий служит крепежом для лезвия, вторая пара используется для закрепления проводов выжигателя. На вторую пару будет приходить электрический ток. Третья пара отверстий необходима для болта, с помощью которого будут стягиваться вместе две пластины.
- Для закрепления ручки устройства нужно высверлить еще по два отверстия в пластине. Центры этих четырех отверстий располагаются перпендикулярно осям вышеописанных крепежных отверстий. Лучше изготовить ручку из деревянного бруса, в котором предварительно просверливаются отверстия для прикручивания ее к пластинам при помощи двух болтов.
Самодельные приспособления, с помощью которых можно нарезать протектор имеют такие недостатки:
- Нагрев прибора не регулируется. Поэтому заметив, что устройство перегрелось его стоит отключить от сети.
- В случае с самодельным регрувером из выжигателя есть вероятность поражения электрическим током: болты, на которые приходит электроток неукрытые изолирующим материалом. Сделать изоляцию для указанных болтов невозможно: любой изолирующий материал расплавится из-за нагрева. Нужно проявить предельную осторожность при работе с указанным прибором.
- При перегреве резина начинает плавиться и гореть. Нарезая протектор нужно следить за чистотой срезов, внешний вид срезов должен быть таким, как будто канавки нарезались не раскаленным, а холодным ножом. В противном случае поплавленный протекторный слой прослужит недолго.
Как согнуть лезвие не сломав его?
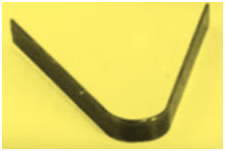
Лезвие для регрувера
При изготовлении самодельного приспособления для нарезки протектора важную роль играет нож либо лезвие, с помощью которого будет разрезаться резина. Нож для указанных целей должен быть очень острым и тонким. При изготовлении регрувера из паяльника можно брать канцелярский ножик, предназначенный для резки бумаги. В случае с выжигателем лучше использовать бритву, она имеет меньшее сечение лезвия, чем ножик, поэтому нагреется быстрее. Учтите: при попытке согнуть нож либо бритву в виде буквы U хрупкий метал, скорее всего, сломается. Избавиться от этой проблемы можно, если предварительно обжечь материал, из которого изготовлен нож либо бритва. Такая термообработка позволяет увеличить пластичность металла: снижает хрупкость.
Для обжига вам понадобятся:
- пассатижи;
- горелка;
- бритва либо лезвие ножа.
Выполняется обжиг в следующей последовательности:
- Лезвие прогревается над огнем до температуры 400 0 С. Узнать, что материал достаточно нагрет можно по красноватому оттенку, который приобретет металл. Различить этот оттенок проще в темном помещении.
- После разогрева материалу нужно дать остыть на открытом воздухе около 6 минут.
Эта процедура увеличит пластичность лезвия, позволит его согнуть под необходимым углом. Указанный угол зависит от нужной формы канавок протектора, он может иметь различную форму, в большинстве случаев это английская буква U.
После придания лезвию нужной формы, внутрь его наружных частей укладывается деревянный брусок, затем эта конструкция зажимается тисками. Далее в лезвии высверливается отверстие для крепежного болта.
Процедура нарезки протекторного слоя
Перед нарезкой протектора шин необходимо выполнить такие подготовительные работы:
- Демонтаж покрышки.
- Осмотр резины на наличие соответствующей маркировки и степень износа. Нарезать можно резину, не имеющую повреждений протектора, бортов и боковины. Плюс степень ее износа определяется по индикатору, присутствующему на поверхности автопокрышки, если остаточная глубина меньше 3 мм, то ремонтные работы не проводятся, есть вероятность повреждения кордового слоя изделия при нарезке протектора.
- Очистка покрышки от загрязнений, камушков.
- Устранение мелких повреждений шины, если такие присутствуют.
- Определение параметров нарезки: выбор ширины и глубины канавок. Глубина лезвия устанавливается по минимально допустимой высоте канавки.
Проводить нарезку шин нужно с хорошей скоростью, если работать медленно, то резина начнет плавиться. Нарезают протектор полосками по 15 см в направлении канавок протекторного слоя. Срезанный материал незамедлительно удаляют. По окончании восстановительных работ нужно очистить поверхность покрышки от остатков залипшей резины.
Заключение
Нарезать протектор шин можно собственными руками, указанная процедура не занимает много времени. Для проведения восстановительных работ понадобится специальный инструмент — регрувер, рыночная стоимость которого довольно высокая. Покупать для домашнего пользования заводской регрувер нецелесообразно, так как нарезается протекторный слой максимум два раза в год. При желании можно изготовить устройство для нарезки в домашних условиях из подручных материалов — это позволит значительно сэкономить бюджет.
Нарезая глубину протектора необходимо придерживаться рекомендованных норм, иначе можно повредить кордовый слой покрышки и она будет непригодна для эксплуатации.
Нарезать резину на покрышках легковых автомобилей не рекомендуется — восстановленные таким способом шины недопустимо применять на высоких скоростях, есть вероятность разрыва автошины во время езды. Объясняется такая ситуация отсутствием на автопокрышках легковых машин дополнительного резинового слоя. Если попытаться восстановить протектор таких шин нарезкой, то каркас резины утратит жесткость. Нарезают покрышки, имеющие соответствующую маркировку, нанесенную на их поверхность заводом-изготовителем.
Для чего нужен протектор? Правильно, для обеспечения сцепления колеса с дорогой.
Но что делать, если стертый рельеф шины не дает должного уровня сцепления? В этом случае нужно взять грувер для нарезки протектора и восстановить уровень сцепления. Как это сделать? Об этом читайте в нашей статье.
Как восстановить резину
Заводская нарезка ламелей в автомобильных шинах предполагает создание канавок с достаточным углублением, но со временем их высота тает, стираясь об асфальт и грунтовое покрытие.
Минимально допустимая глубина накатки не может быть меньше:
- 1,6 миллиметра у легковых авто;
- 1 миллиметра у грузовых автомобилей;
- 2 миллиметров у автобусов;
- 0,8 миллиметра у мотоциклов.
Если покрышка стерлась до вшитого в резину маркера, то придется купить новую автошину. Хотите избежать лишних трат — попробуйте нарезать новые углубления в толстой резине до того, как ее высота опустится ниже 0,8-2,0 миллиметра.
Чтобы восстановить резину, вам понадобится специальный нож-грувер и хороший глазомер. При наличии навыков и специального инструмента, вы сможете нарезать протектор своими руками буквально за один-два часа, сэкономив неплохие деньги. Однако такая технология работает далеко не со всеми автошинами.
Фото шины автомобиля марки УАЗ до нарезки
Фото шины УАЗ после нарезки
Какие виды шин можно восстанавливать
Повсеместное увлечение экологией и угроза глобального потепления климата изменила судьбу изношенных колес. Раньше такие покрышки образовывали рукотворные горы на каждой свалке. Сегодня, согласно распространенным в Евросоюзе требованиям, обязательному восстановлению подлежат следующие виды автошин:
- грузовые покрышки формата R-16С — R-22.5;
- все цельнолитые шины на спецтехнику;
- большинство болотных (грязевых) покрышек для внедорожников.
Восстановление грузовых автошин и болотных автопокрышек для внедорожников возможно только при содействии производителя, предусмотревшего совместимость с технологией нарезки на этапе производства резины. Поэтому разрезать шины в домашних условиях можно только в том случае, если на их бортах читается надпись — REGROOVABLE.
Если вы не видите такой надписи — обратитесь в автомастерскую или откажитесь от идеи восстановления протектора. Ведь колесо легкового авто качают до 2,5 атмосферы, а в покрышку грузовика задувают до 8 бар, поэтому даже малейшая ошибка при нарезке снизит срок службы шины в несколько раз.
Оборудование для резки ламелей
Прежде чем нарезать новые углубления на протекторе, вам нужно найти подходящий случаю прибор. В автомастерских для этих целей используют особый станок для автомобильных шин, а домашнее мастера предпочитают резать покрышку руками, используя ножи или машинки.
Самая популярная машинка для нарезки протектора — электрический регрувер. Этот гибрид ножа и паяльника режет канавки глубиной от 0,5 до 5 миллиметров, формируя новый рисунок протектора. Перед таким резаком не устоит даже литая покрышка. Причем комбинированное (тепловое и механическое) воздействие на резину не предполагает больших усилий при резке. Профессиональный прибор для восстановления ламелей отличается от инструмента для гаражных умельцев возможностью менять режущие насадки. Производители таких машинок выпускают особые комплекты насадок для каждого бренда легковых или грузовых автомобильных шин. Некоторые инструменты позволяют нарезать в одно движение сразу несколько ламелей.
Как сделать покрышку устойчивее на дороге — основы процесса нарезки
Уменьшение глубины протектора снижает сцепление автошины с дорогой, поэтому для повышения устойчивости нужно углубить существующие канавки, не расширяя их. Для этих целей вам нужно найти специальную насадку на регрувер или изготовить самодельный нож для легковых покрышек и грузовых протекторов.
Если покрышки нарезают автомобильным регрувером, инструмент перемещается от центра протектора к его краю. При этом нужно контролировать положение локтя — он должен оставаться в плоскости, параллельной пятну контакта. Если вы поднимите или опустите локоть во время реза — на протекторе появится лишняя ямка или невыбранный по глубине участок.
Читайте также: