Защита от коррозии двигателя и системы выпуска газов
Защита от коррозии двигателя и системы выпуска газов
Система выпуска газов современных автомобилей работает в тяжелых условиях. Изнутри ее разрушают горячие отработавшие газы, пары кислот, конденсат влаги, а снаружи — вода, грязь, соль, камни. Кроме того, тенденция к уменьшению высоты современного автомобиля приводит к тому, что его выпускная система приближается к дорожному полотну, вследствие чего глушитель и трубы корродируют быстрее.
Можно выделить пять основных видов коррозии:
местная в местах сварки, щелях, зазорах;
под влиянием механических нагрузок и деформации;
под влиянием высоких температур.
Общая внутренняя коррозия системы выпуска газов развивается вследствие образования при сгорании топлива воды, оксидов углерода, азота и серы. Кроме того, этилированные топлива содержат рафинирующие добавки в виде хлоридов и бромидов, которые являются источниками образования соляной и бромистоводородной кислот.
Коррозия внутренних поверхностей глушителя ускоряется также от действия нагара, образующегося во время работы двигателя.
Эффективным способом защиты от коррозии наружных поверхностей системы выпуска газов является их окрашивание. Однако при этом надо учитывать, что температура отработавших газов, измеренная у выпускного трубопровода, обычно находится в пределах 420. 760°С, а металл выхлопной трубы нагревается соответственно до 240. 540°С, т. е. для их окрашивания пригодны
только термостойкие, в основном кремнийорганические эмали и лаки.
Термостойкость лаков значительно повышается при добавлении к ним 6. 10 % алюминиевой пудры. Причем смешивать пудру с лаком нужно непосредственно перед употреблением, так как при длительном хранении (более 4. 6 ч) пудра теряет способность всплывать. В результате ухудшаются эксплуатационные показатели и внешний вид покрытия.
Специально для окрашивания деталей системы выпуска отработавших газов автомобиля предназначены эмали КО-828 и КО-813 цвета алюминия. В качестве растворителя для них используют сольвент или РКБ-1.
Двигатель автомобиля окрашивают нитроглифталевой эмалью с алюминиевой пудрой или эмалью МС-17 светло-серого цвета. Перед употреблением в эмаль МС-17 добавляют 2 % сиккатива № 63 или № 64.
В процессе эксплуатации двигатель может нагреваться до 80°С. При этом масла, пыль, сажа и другие загрязнения скапливаются и создают довольно толстую пленку, которая, являясь хорошим теплоизолятором, затрудняет охлаждение двигателя.
Используя «Автоочиститель двигателя», можно быстро и качественно очистить его поверхность. В состав очистителя входят растворители, поверхностно-активные вещества, ингибиторы коррозии и др.
KROWN › Блог › Методы защиты от коррозии в автомобилестроении
Как мы уже говорили, проблема изыскания новых и совершенствование старых способов защиты от коррозии актуальна, как для всей тяжёлой промышленности в целом, так и для автомобильной отрасли в частности.
Еще в XIX веке лучшие инженерные умы того времени волновала проблема защиты металлических конструкций от ржавления. Например, Александр Гюста́в Э́йфель, отец и создатель знаменитой «Tour de 300 mètres», говорил: «Трудно переоценить роль краски в сохранении металлического сооружения, и забота об этом – единственная гарантия его долголетия».
Кстати, вот уже 131 год эта достопримечательность Парижа противостоит воздействию неблагоприятных факторов окружающей среды именно благодаря краске. Интересный факт – для защиты 200.000 м2 наружной поверхности башни используется около 60 тонн специальной краски. Покраской занимается обслуживающая Эйфелеву башню специально созданная компания «SETE» («Société Nouvelle d’exploitation de la Tour Eiffel»). Весь процесс окраски занимает около 18 месяцев! Вначале, все детали конструкции тщательно осматриваются. Те, на которых слой антикоррозионного покрытия нарушен, – очищаются от старого и покрываются новым. Кроме того, вся поверхность сооружения перед окраской очищается паром высокого давления. Красят башню в два слоя.
Но, окрашивание защищаемой поверхности – всего лишь один из способов защиты металла от коррозии. Применительно к автомобилестроению, все методы защиты можно условно разделить на следующие виды:
1. Нанесение защитных покрытий (металлических и неметаллических).
2. Изменение характеристик коррозионной среды.
3. Легирование.
4. Электрохимическая защита
5. Рациональное конструирование.
Нанесение защитных покрытий
Нанесение защитных покрытий – один из самых простых, а также исторических старых способов защиты металла от коррозии. Различают металлические и неметаллические покрытия. В свою очередь неметаллические покрытия делят на органические и неорганические.
Органические покрытия – это, привычные нам, лак и краска, а также разнообразные смолы. Сюда же относят полимерные плёнки и резину.
Неорганические покрытия включают в себя разнообразные эмали и грунты на основе соединений кремния, фосфора, цинка и хрома, а также оксидов металлов (например, оксид титана). Классическим примером использования неорганического покрытия в автомобилестроении является процесс фосфатирования автомобильных кузовов. Так, слоем фосфатов перед покраской покрывают кузова автомобилей на заводах Mercedes-Benz.
Металлические покрытия (анодные и катодные) представляют собой нанесённый на защищаемую поверхность слой металла (цинк, хром, кадмий, алюминий и др.) или металлического сплава (олово, бронза, латунь и т.д.). У анодного покрытия электродный потенциал меньше электродного потенциала защищаемого металла. Поэтому, при повреждении анодного покрытия в первую очередь будет окисляться непосредственно оно само. В случае с катодным металлическим покрытием – наоборот: электродный потенциал покрытия выше потенциала защищаемого металла. Значит, при повреждении такого покрытия первой будет окисляться сама защищаемая поверхность.
Применительно к автомобилестроению, классическим примером защиты с помощью металлического покрытия является оцинкованный автомобильный кузов. Этот способ получил очень широкое распространение и на сегодняшний день целый ряд автопроизводителей используют цинкование для защиты кузовных деталей. Но, первопроходцем в этом деле стала немецкая компания Audi, впервые применившая оцинковку для защиты кузовов своих автомобилей. Не остановившись на этом, инженеры Audi AG разработали и внедрили в производство двухстороннюю цинковую защиту не только кузовных деталей, но и их сварных соединений, а также и самих кузовов в целом. (Метод т.н. «горячего» цинкования погружением в ванну.) Первым серийным автомобилем с полностью оцинкованным кузовом стал Audi 80 B3, впервые сошедший с конвейера в уже далеком 1986 году.
Изменение характеристик коррозионной среды
Изменение характеристик коррозионной среды – суть этого метода защиты заключается в том, что для снижения агрессивности среды в ней уменьшают количество опасных в коррозионном отношении компонентов или же применяют ингибиторы коррозии. (Это специальные вещества, замедляющие её скорость.) И вот, казалось бы, неразрешимая дилемма – как можно снизить количество опасных для стальных деталей автомобиля химических соединений в городской среде? Да очень просто – для начала перестать сыпать на дороги зимой активаторы коррозии, к примеру, тот же хлорид натрия. (О его роли в химическом процессе ржавления автомобиля мы говорили в первой части нашего рассказа.)
Что касается ингибиторов коррозии, то их целесообразно использовать в замкнутых системах (где редко или мало обновляется циркулирующая жидкость). В автомобилестроении типичным примером таковой является система охлаждения двигателя. А все современные антифризы в обязательном порядке содержат в себе ингибиторы коррозии.
Легирование
Легирование (от немецкого legieren – «сплавлять» и от латинского ligare – «связывать») – один из самых эффективных и, одновременно, дорогих способов борьбы со ржавчиной. Суть этого метода заключается в том, что в состав стали добавляют т.н. «легирующие элементы». Таковыми являются некоторые металлы: хром, никель, марганец, ванадий, ниобий, вольфрам, молибден, титан, медь. Данные компоненты придают сплаву пассивность – т.е. при начале коррозии образуются плотные поверхностные продукты реакции, предохраняющие металл от дальнейшего коррозионного разрушения.
Легированные стали, устойчивые к коррозии в атмосфере и агрессивных средах, также называют «нержавеющими сталями», или же, в простонародье, «нержавейкой». Если говорить об её применении в машиностроении, то нужно сказать, что изготовить кузов автомобиля целиком из нержавеющего сплава, конечно же, возможно. Вот только никакой целесообразности в этом нет, ибо цена такой машины будет астрономической. Причина – изначально высокая стоимость коррозионно-стойкой стали. Тем не менее, в автомобилестроении она активно используется. Так, из неё изготавливают детали системы выпуска отработанных газов и термоотражающие экраны.
Электрохимическая защита
Если говорить о методе электрохимической защиты, то, применительно к автомобилестроению, он является малоиспользуемым. Его суть заключается в торможении протекающих при электрохимической коррозии процессов (катодного / анодного). Например, к защищаемому элементу присоединяется деталь из более активного, нежели сам элемент, металла. В образовавшейся гальванической (коррозионной) паре в первую очередь будет разрушаться активный металл (протектор).
А вот метод рационального конструирования, в силу своей относительной простоты и малозатратности, наоборот, получил широкое распространение в машиностроении. Суть его заключается в том, что при проектировании узлов и агрегатов по возможности пытаются уменьшить площадь контакта с агрессивной средой опасных в коррозионном отношении участков деталей (сварных швов и металлических соединений). Если, в силу особенностей конструкции, сделать это не представляется возможным, предусматривают защиту данных узлов от коррозии различными вышеуказанными методами.
___________
Krown — ЗА НАМИ НЕ ЗАРЖАВЕЕТ
Центр антикоррозийной защиты автомобилей
Защита от коррозии двигателя и системы выпуска
Система выпуска газов современных автомобилей работает в тяжелых, способствующих коррозии условиях. Изнутри ее разрушают горячие отработавшие газы, пары кислоты и конденсата влаги, а снаружи - вода, грязь, соль, камни. Кроме того, тенденция к уменьшению высоты современного автомобиля приводит к тому, что его выпускная система приближается к дорожному полотну, вследствие чего глушитель и трубы коррозируют еще быстрее.
Из большого количества эксплуатационных факторов, способствующих коррозии, можно выделить пять основных: общая внутренняя коррозия; общая внешняя коррозия; местная коррозия в местах сварки, щелях и зазорах; коррозия под влиянием механических нагрузок идефор майки; коррозия под влиянием высокой температуры.
Файлы: 1 файл
ЗАЩИТА ОТ КОРРОЗИИ ДВИГАТЕЛЯ И СИСТЕМЫ ВЫПУСКА.docx
ЗАЩИТА ОТ КОРРОЗИИ ДВИГАТЕЛЯ И СИСТЕМЫ ВЫПУСКА
Система выпуска газов современных автомобилей работает в тяжелых, способствующих коррозии условиях. Изнутри ее разрушают горячие отработавшие газы, пары кислоты и конденсата влаги, а снаружи - вода, грязь, соль, камни. Кроме того, тенденция к уменьшению высоты современного автомобиля приводит к тому, что его выпускная система приближается к дорожному полотну, вследствие чего глушитель и трубы коррозируют еще быстрее.
Из большого количества эксплуатационных факторов, способствующих коррозии, можно выделить пять основных: общая внутренняя коррозия; общая внешняя коррозия; местная коррозия в местах сварки, щелях и зазорах; коррозия под влиянием механических нагрузок идефор майки; коррозия под влиянием высокой температуры.
Общая внутренняя коррозия системы выпуска разиваст-ся вследствие образования при сгорании топлива воды, окислов углерода, азота и серы Все эти вещества являются сильными окислителями метал па. Кроме того, этилированные топлива содержат рафинирующие добавки в вице хлоридов и бромидов, которые являются источником образования со ляной и бромистоводородкой кислот.
Коррозия внутренних поверхностей глушителя ускоряется также от действия нагара, образующегося во время работы двигателя. Вследствие большого различия коэффициентов теплового расширения слоя нагара и материала глушителя слой нагара при резких перепадах температур (например, при попадании на наружную поверхность глушителя воды) подвергается большим внутренним напряжениям и частично отслаивается. Открывается незащищенная поверхность мета-ии которая легко корродирует.
Коррозия наружных поверхностей выпускной системы вызывается повышением температуры металла от контакта с отработавшими газами, а также воздействием водяных брызг, соли и грязи. Кроме того, при движении автомобиля от вибрации двигателя в глушителе и других деталях выпускного тракта возникают усталостные напряжения, ускоряющие процесс их коррозии.
Эффективным способом защиты от коррозии наружных поверхностей системы выпуска является их окрашивание Однако при этом надо учитывать, что температура отработавших газов, измеренная > выпускного трубопровода, обычно находится в пределах 420-760 °С, а температура металла выхлопной трубы составляет соответственно 200—540 °С [24|. Поэтому для их окрашивания пригодны только термостойкие, в основном кремнийорганическне эмали и лаки.
Термостойкость последних значительно повышается при добавлении к ним 6- 10 7 алюминиевой пудры Смешивать пудру с лаком нужно непосредственно перед употреблением, гак как при длительном хранении (более 4-6 ч) пудра теряет способность всплывать. В результате ухудшаются эксплуатационные показатели и внешний вид покрытий
Кремнийорганическне эмали и лаки после добавления к ним алюминиевой пудры имеют следующую термостой кость: КО-83 до 420 °С, КО-88 и КО 815 до 500 "С, КО-811 и KO-8I4- до400°С [7].
Специально для окрашивания деталей системы выпуска отработавших газов автомобиля предназначены эмали КО-828 и КО-813 алюминиевого цвета Покрытия из эмали КО-82Б обладают хорошей адгезией, соле- и влагостойкостью, выдерживают температуру +400 С Ее наносят методом пневматического распыления без предварительного грунтования поверхности двумя слоями способом "мокрый по мокрому", с промежуточной выдержкой на воздухе в течение 5 мин ► сушат в течение 30 мин при 130 °С. В качестве растворите лей используют сольвент или РКБ-1.
Эмаль КО-813 перед пневмораспылением разводят толуолом до вязкости 12—13 с а сушат при 150 °С в течение 2 ч
Лак КО-83 после смешивания с алюминиевой пудрой сохраняет жизнеспособность в течение 6 ч. При нанесении из краскораспылителя его нужно развести до вязкости 13— 14с ^- «1по ВЗ 4 растворителем № 646. Сушат его-«ри 170-180 "С в течение 2 ч.
Эмали КО-Ы1 выпускают красного, черного и зеленого цветов. Высыхают они за 2 ч при 200 °С. Разводят их разжи-житслем Р-5. Вязкость при распылении 12—15 с.
Высокой термостойкостью обладают покрытия из полиамидных лаков. Они имеют хорошую адгезию к металлам и стойки к абразивному износу. Добавление в них 20 9< алюминиевой пудры значительно повышает термостойкость покрытий.
Автолюбители используют и другие способы защиты системы выпуска. Например, для предохранения от коррозии наружных поверхностей выпускных труб и глушителя автомобиля их очищают от грязи и рыхлой ржавчины, а затем покрывают тонким слоем графитовой смазки. После того как она обгорит, детали оказываются покрыты довольно прочной термостойкой противокоррозионной пленкой черного цвета [25].
Двигатель автомобиля окрашивают нитроглифталевой эмалью с алюминиевой пудрой или эмалью МС-17 светлосерого цвета. Перед употреблением в эмаль МС-17 нужно добавить 2 % сиккатива Н° 63 или 64 (18].
Поверхность двигателя в процессе эксплуатации может нагреваться до 80 с С. Масла, пыль, сажа и другие загрязнения, скапливаясь на различных частях двигателя, образуют смесь, которая под воздействием тепла постепенно превращается в плотную, довольно толстую пленку. Эта пленка является хорошим теплоизолятором и затрудняет процесс естественного охлаждения двга атсля за счет теплообмена с воздухом. Зимой это незаметно, а летом, особенно в южных районгх, может стать прямой причиной ухудшения работы двигателя: снижения мощности, повышения расхода топлива, преждевременного износа.
Опытные водители [27] с целью очистки двигателя от грязи и для его противокоррозионной зашиты советуют ! раз в две недели протирать блок, крышку распределительного вала, кожух вентилятора, поддон и другие детали двигателя ветошью, обильно смоченной в моторном масле, а затем насухо вытирать двигатель чистой тряпкой. Если же грязь уже накопилась, то ее можно снять с помощью скребков, щеток и тряпок Однако это весьма трудоемкий процесс да и качество очистки не очень хорошее. Поэтому на авторемонтных предприятиях для этой цели применяют водные моющие растворы, состоящие из смеси три-натрий фосфата, кальцинированной соды, метасиликата натрия и др. Двигатель снимают с автомобиля и погружают в горячий (70—90 °С) моющий раствор. При комнатной температуре этот раствор малоэффективен, поэтому в условиях индивидуального гаража непригоден. Растворители, обычно используемые для обезжиривания, если слой грязи старый и плотный, тоже не полностью удаляют загрязнения, а посте их применения на поверхности двигателя зачастую остается тонкая липкая пленка, содержащая остатки масел и смолистых веществ. К этой пленке легко пристает пыль, и двигатель снова быстро загрязняется.
Промышленность выпускает "Автоочиститель двигателя", позволяющий быстро и качественно очистить его поверхность. В состав очистителя входят растворители, поверхностно-активные вещества, ингибиторы коррозии и др. Очиститель хорошо снимает с двигателя все загрязнения и не оказывает отрицательного воздействия на металл. "Автоочиститель двигателя" пожароопасен, поэтому до нанесения препарата на двигатель необходимо отключить провода от клемм аккумуляторной батареи, чтобы предотвратить возможность искрения.
Лучше всего проводить очистку двигателя на открытой площадке, оборудованной коммуникацией для отвода сточных вод и краном с холодной водой. На поверхность двигателя очиститель наносят малярной кистью или распылением. Особенно тщательно препарат нужно наносить на места, где много грязи. Состав выдерживают некоторое время на поверхности и затем смывают водой из шланга. Если двигатель очень загрязнен и одноразовой обработки не хватает, сильно загрязненные места обрабатывают повторно
После окончания обработки двигатель нужно тщательно обмыть водой из шланга до полного удаления остатков загрязнений. Если двигатель обмывают водой из ведра или лейки, то для промывки необходимо 40-50 л воды [5] Во всех случаях двигатель необходимо мыть водой до тех пор, пока полностью не исчезнут следы эмульсии и пены.
Делаем долговечный антикор выхлопной системы за 30 минут и 1000 рублей. Делюсь способом
Выхлопная система - часть автомобиля, наиболее подверженная образованию коррозии. Даже по сравнению с днищем и колёсными арками ржавчина на ней появляется быстрее. Высокая влажность, реагенты и другие негативные факторы быстро приводят металл в негодность. Классические методы антикоррозийной обработки для выхлопной системы не подходят. Из-за высокой термонагруженности нужно применять специальные технологии. Я расскажу о самой простой и доступной из них.
Днище и колёсные арки автомобиля принято защищать доступными средствами, которые продаются в любом крупном строительном магазине. Для этих целей хорошо подходит смесь мастики и пушечного сала, обладающая прочностью и эластичностью. Однако, на выхлопную систему автомобиля её наносить нельзя . Под воздействием высокой температуры материал потеряет свою твёрдость и быстро "сползёт" с поверхности.
Замена выхлопной системы - недешёвая процедура. Многие автолюбители подваривают прогоревший металл, но это даёт лишь временный результат. Намного лучше заранее позаботиться о защите выпускной системы, до появления на ней очагов ржавчины. Сейчас не составит труда купить термоустойчивые материалы, которые обеспечат длительное противодействие коррозии . Стоят они недорого, а нанести их можно даже без наличия опыта.
Первым делом рекомендую осмотреть банки глушителя на наличие дренажной системы. На многих автомобилях она не предусмотрена заводом-изготовителем. Конденсат, скапливающийся в банках, замерзает при длительной стоянке автомобиля и оттаивает после прогрева. Высокая влажность активизирует коррозийные процессы , из-за чего выхлоп "разъедает" изнутри. Проделать дренаж можно самостоятельно, выполнив небольшое отверстие в банке глушителя.
Далее переходим к защите остальной части выпускной системы от коррозии. Первым делом следует очистить днище от грязи и иных твёрдых отложений. Мойку выхлопа можно произвести самостоятельно или заказать такую услугу в организации . На многих автоматизированных мойках предусмотрена функция очистки днища. Затем выхлопная система тщательно обезжиривается, удобнее всего производить процедуру на яме, эстакаде или подъёмнике. При отсутствии такой возможности нужно максимально высоко поддомкратить автомобиль и подложить твёрдые предметы под пороги.
Обеспечивать защиту выхлопной системы будет термолак. Один баллончик материала стоит примерно 1000 рублей, его вполне достаточно для обработки одного автомобиля. Термолак выдерживает температуру до +800 градусов, поэтому отлично подходит для наших целей . Материал наносится в несколько слоёв, после чего запускается двигатель для прогрева выпускной системы. Под воздействием температуры лак полимеризуется и быстро застывает. На практике такой защиты хватает на 3-5 лет городской эксплуатации автомобиля. Нанести материал можно всего за полчаса.
72 Защита от коррозии двигателя и системы выпуска газов
Система выпуска газов современных автомобилей работает в тяжелых условиях. Изнутри ее разрушают горячие отработавшие газы, пары кислот, конденсат влаги, а снаружи — вода, грязь, соль, камни. Кроме того, тенденция к уменьшению высоты совре менного автомобиля приводит к тому, что его выпускная система приближается к дорожному полотну, вследствие чего глушитель и трубы корродируют быстрее.
Можно выделить пять основных видов коррозии:
местная в местах сварки, щелях, зазорах;
под влиянием механических нагрузок и деформации;
под влиянием высоких температур.
Общая внутренняя коррозия системы выпуска газов развивает ся вследствие образования при сгорании топлива воды, оксидов углерода, азота и серы. Кроме того, этилированные топлива со держат рафинирующие добавки в виде хлоридов и бромидов, ко торые являются источниками образования соляной и бромистово-дородной кислот.
Коррозия внутренних поверхностей глушителя ускоряется так же от действия нагара, образующегося во время работы двигателя.
Эффективным способом защиты от коррозии наружных по верхностей системы выпуска газов является их окрашивание. Од нако при этом надо учитывать, что температура отработавших газов, измеренная у выпускного трубопровода, обычно находится в пределах 420. 760°С, а металл выхлопной трубы нагревается соответственно до 240. 540 °С, т. е. для их окрашивания пригодны только термостойкие, в основном кремнийорганические эмали
Термостойкость лаков значительно повышается при добавле нии к ним 6. 10 % алюминиевой пудры. Причем смешивать пудру с лаком нужно непосредственно перед употреблением, так как при длительном хранении (более 4. 6 ч) пудра теряет способ ность всплывать. В результате ухудшаются эксплуатационные пока затели и внешний вид покрытия.
Специально для окрашивания деталей системы выпуска отрабо тавших газов автомобиля предназначены эмали КО-828 и КО-813 цвета алюминия. В качестве растворителя для них используют сольвент или РКБ-1.
Двигатель автомобиля окрашивают нитроглифталевой эмалью или яма лью МС-17 светло-серого цвета. Перед употреблением в эмаль МС-17 добавляют 2 % сиккатива № 61
В процессе эксплуатации двигатель может нагреваться до 80 °С. При этом масла, пыль, сажа и другие загрязнения скапливаются и создают довольно толстую пленку, которая, являясь хорошим теп-лоизолятором, затрудняет охлаждение двигателя.
Используя «Автоочиститель двигателя», можно быстро и каче ственно очистить его поверхность. В состав очистителя входят ра створители, поверхностно-активные вещества, ингибиторы кор розии и др.
73 Защита от коррозии днища, шасси и скрытых полостей автомобиля
В настоящее время лучшими защитными материалами для дни ща и крыльев автомобиля считаются поливинилхлоридные пластизоли. Срок их действия от 3 до 7 лет. На автозаводах из материа лов этого класса обычно используют пластизоль Д-11А. Покрытия из него обеспечивают также уменьшение шумов при движении автомобиля. Пластизоль наносят методом безвоздушного распыле ния и высушивают при 130 °С в течение 30 мин.
К этому же классу относятся битумные и каучуковые покрытия. Битумные покрытия защищают металл 1. 2 года. Они хорошо про тивостоят действию соли, воды и влаги, но недостаточно стойкие к ударам камней, щебня и морозу.
В настоящее время из отечественных противокоррозионных по крытий выпускаются «Автоантикор-2 битумный для днища», мас тика сланцевая автомобильная МСА-3, автоантикор для днища резинобитумный, мовиль, «Мольвин-МЛ», «Резистин» и др. Все составы обладают хорошей смачивающей способностью, легко проникают в дефекты сварочных швов, трещины, узкие зазоры
между листами металла, а также в рыхлую ржавчину, пропитывая ее и замедляя процесс коррозии там, где он уже начался.
Защитное покрытие системы выпуска
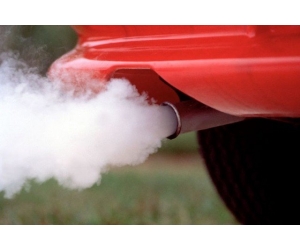
Система выпуска газов у нынешних автомобилей, к сожалению, функционирует в условиях, которые способствуют развитию коррозии. Система разрушается не только снаружи водой, грязью, солью, камнями, но и изнутри отработавшими газами, парами кислоты и конденсатом влаги. На разрушение выпускной системы влияет и тенденция к снижению высоты легковой машины — система находится близко к дорожному полотну и в результате трубы и глушитель разрушаются еще быстрее.
Выделим основные эксплуатационные факторы, которые способствуют коррозии: это сплошная внешняя коррозия; коррозия, образовавшаяся под действием деформации и нагрузок; сплошная внутренняя коррозия; коррозия, образовавшаяся из-за высокой температуры; местная коррозия, образовавшаяся в местах сварки, в зазорах и щелях.
Причиной сплошной внутренней коррозии становятся образования, которые появляются при сгорании топлива, азота, воды, окислов углерода и серы. Стоит отметить, что некоторые из них считаются сильными окислителями металла. Помимо этого, в этилированном топливе содержатся рафинирующие добавки в виде бромидов и хлоридов. Эти добавки образуют соляную и бромисто-водородную кислоты.
Коррозия глушителя изнутри ускоряется за счет влияния нагара, который образуется во время работы мотора. При резкой смене температур слой нагара подвергается большим напряжениям, так как коэффициент теплового расширения материала глушителя и слоя нагара сильно отличается, отчего он начинает отслаиваться, открывая при этом ту поверхность металла, которая не защищена, поэтому она быстро и легко ржавеет.
Причины разрушения наружной поверхности выпускной системы — увеличение температуры металла от соприкосновения с отработавшими газами. Другая причина разрушения — это попадание на поверхности системы соли, водяных брызг, грязи.
Чтобы хоть как-то систему выпуска и двигатель защитить от коррозии применяют разные способы. Например, в США и в некоторых других странах 90% глушителей производят из алюминированной стали. На поверхность такой стали диффузионным методом наносится смесь порошков оксидов алюминия и алюминия. Долговечность глушителя при этом возрастает раза в два-три. В Великобритании для изготовления глушителей берут сталь, в которой содержатся 36% титана и 11% хрома. Еще для изготовления глушителей идет сталь, легированная молибденом.
Наиболее эффективно защищает наружные поверхности системы выпуска от коррозии их окраска. Однако окрашивая поверхности системы нужно брать во внимание, что температура отработавших газов у выпускного трубопровода колеблется от 420°С до 760°С. Тогда как температура металла выхлопной трубы колеблется от 200°С до 540°С. Следовательно, окрашивать систему выпуска следует исключительно термостойкими, в основном кремнийорганическими лаками и эмалями. Термостойкость лака можно увеличить добавлением 6-10% алюминиевой пудры. Пудра добавляется в лак исключительно перед его применением, потому что пудра при длительном хранении (больше 4 часов) начинает терять свою способность всплывать, из-за чего ухудшается внешний вид покрытий и эксплуатационные показатели. Термостойкость кремнийорганических лаков и эмалей после добавления алюминиевой пудры такова: КО-811, а также КО-814 — до четырехсот градусов; КО-88, а также КО-815 – до пятисот градусов; КО-83 – до 420 градусов.
Эмаль КО-828 имеет алюминиевый цвет и используется для окраски поверхностей системы выброса. Поверхности, обработанные этой эмалью, имеют хорошую адгезию, влагостойкость и солестойкость и могут выдержать температуру до 400°C. На поверхности системы эмаль наносится методом пневматического распыления, а в качестве растворителя используется РКБ-1 или сольвент. Покрытие сушится в течение получаса при 130°C.
Подобная эмаль наносится на металл двумя слоями, при этом грунт наносить не нужно. Наносится слой эмали, потом 5 минут выдержки на воздухе и наносится второй слой эмали.
Если алюминиевая пудра была добавлена в лак КО-83, то его нужно использовать в течение 6 часов. Если лак наносится при помощи краскораспылителя, то он разводится растворителем №646 до такой вязкости 13-14 с по B3–4. Окрашенное покрытие сушится в течение двух часов при температуре 170-180°.
Эмали КО-811 бывают зеленого цвета, черного и красного цвета, при температуре 200 градусов высыхают в течение двух часов. При распылении вязкость должна быть 12–15 с по В 3–4.
Поверхности, покрытие полиамидным лаком, имеют достаточно высокую термостойкость, адгезию к металлам. Такие поверхности также обладают хорошей стойкостью к абразивному износу. Термостойкость покрытий значительно увеличивается за счет добавления 20% алюминиевой пудры.
Также существуют и другие методы защиты системы выпуска от коррозии, которыми пользуются и автолюбители и мастера. Например, такой — поверхность глушителя и выпускной трубы очищается от рыхлой ржавчины и грязи, затем покрывается графитовой смазкой (наносить нужно тонким слоем). После того, как смазка обгорит, она оставит после себя прочную противокоррозионную пленку черного цвета, которая и защитит детали от коррозии.
Рыжая болезнь. Как защитить автомобиль от коррозии
Ржавчина, коррозия, окисление… Пожалуй, что пока при сборке машин используют железные детали, эти слова будут неприятны всем автомобилистам. Как же бороться с коррозией и защитить свой автомобиль от этой “болезни”?
Коррозия и где она образуется
Коррозия - это химическая реакция окисления (разрушения) железа, которая происходит при наличии двух главных героев - воды и кислорода. Некачественное лакокрасочное покрытие, механические повреждения на нем, различные стыки, швы кузова, элементы выхлопной системы и трансмиссии, а также слабо вентилируемые полости автомобиля - самые уязвимые места для ржавчины.
А ускоряет процесс коррозии не только количество попадающей на металлические детали влаги, но и повышенная загазованность воздуха, различные последствия промышленных выбросов, перепады температур, сильные вибрации (появляются микротрещины), а также соль, песок и хлорид кальция (сильнее всего от него страдают хромированные детали) и т.д. При этом нужно понимать, что разные металлические поверхности автомобиля окисляются с различной скоростью. Это зависит не только от местонахождения детали, но и от силы прессинга вышеперечисленных возбудителей ржавчины.
Как же бороться со ржавчиной?
Начнем с того, как автопроизводители сражаются с коррозией. Собственно, существует всего два вида защиты: барьерная (изоляция металла от физического контакта с внешней средой) и протекторная (электрохимическая).
Барьерная защита - это сама краска, а также грунт, лак, мастика и иногда хром. При этом самую мощную защиту от коррозии выполняет именно грунт. На заводе используется так называемое катодное грунтование (катафорез), когда в специальной ванне на кузов подается “минус”, а на грунтовку – “плюс”. Такой способ обеспечивает надежное “прилипание” грунта и очень высокую (в 2-3 раза по сравнению с традиционным нанесением) большую стойкость к коррозии. Кстати, некоторые автопроизводители сверху основного грунта еще наносят слой “филлера”, который заполняет все микропоры, чтобы влага уж точно не смогла подобраться к металлу.
А вот главный принцип протекторной защиты в том, что окисляться (или повреждаться) должен внешний слой цинка (1-9 мкм), находящийся в контакте с металлом. Проще говоря, речь идет о стальном листе с нанесенным на нее покрытием из цинка, которое надежно оберегает металл от ржавления.
К слову, первым серийным автомобилем с полностью оцинкованным кузовом стал седан Audi 80 в 1986 году. Цинкование кузова — процесс недешевый, поэтому некоторые производители бюджетных автомобилей покрывают цинком только те детали, которые находятся, так сказать, на виду.
Как защитить машину?
Думаете, если у вас дорогая машина, то антикоррозийная обработка вообще никогда не потребуется? Ошибаетесь. Внешние воздействия, описанные в начале статьи, никто не отменял. Какие же существуют способы защиты?
Антикоррозийное покрытие. Самый простой способ защиты от ржавчины - антикоррозийное покрытие. Обычно в роли антикора выступают различные мастики (на основе битума, или смол, или воска), но на самом деле они уже уходят в прошлое, так как существует множество современных химических средств, образующих более эффективную защитную пленку, которая гораздо дольше предохраняет части автомобиля от коррозии. В среднем обработку поверхностей и скрытых полостей машины надо проводить не чаще одного раза в 2-3 года.
Сильнее всего, как несложно догадаться, подвержены коррозии нижние поверхности автомобиля, в которые летят камни и песок, выполняющие роль наждачной бумаги.
При выборе антикоррозийных средств не верьте продавцам, которые говорят, что антикор можно наносить прямо на ржавчину. Ни в коем случае! Перед нанесением антикоррозийного материала поверхность обязательно должна быть подготовлена: удалены остатки старого антикора (если он был), влага и ржавчина. Правильная подготовка поверхностей - главная составляющая антикоррозийной обработки.
Обычно, если кузов автомобиля обрабатывают антикором полностью, то делают это сверху вниз. Начиная от подкапотного пространства и багажника, заканчивая арками, полостями дверей, порогами и днищем. При этом на лакокрасочное покрытие средство не наносится.
Электрохимическая (катодная) защита. Этот метод используется, когда от ржавчины нужно защитить труднодоступные места автомобиля. Принцип такой: к кузову автомобиля подключается минусовый контакт, а роль плюсового контакта играет цинковая пластина. На образовавшуюся цепь от аккумулятора подается слабый ток и в результате электрохимических процессов кузов машины оказывается защищенным от коррозии (железная пластина является анодом, а кузов - катодом).
Защита автомобиля от коррозии
Коррозия кузова – появление ржавчины и разрушение металлического кузова автомобиля под ее действием. Для изготовления автомобильных корпусов зачастую используют сталь, которая под действием окружающей среды начинает окисляться, тем самым нарушается структура металла и начинает разрушаться. Восстановление ржавого кузова очень сложный и дорогой процесс, поэтому следует заранее предотвратить разрушающее действие коррозии.
От чего возникает коррозия
В наше время коррозия хоть и не приятная проблема, но зато решаемая. Для борьбы с ней, нужно знать какие части корпуса наиболее подвержены ей, и каков механизм возникновения коррозии, а также какими средствами следует пользоваться для ее устранения. Среднестатистические импортные автомобили рассчитаны на 10 лет эксплуатации при гаражном хранении, и при хорошем качестве дорожного покрытия. В странах СНГ эти два пункта не всегда можно соблюсти. Для предотвращения ржавления корпуса следует знать факторы, которые ей способствуют:
- Состояние дорог. Во время движения по плохой дороге кузов повреждается мелкими камнями, образовывая микроскопические сколы, а при движении по ямам кузов начинает вибрировать, и трещины разрастаются;
- Зимний период. Зимой дороги обрабатываются солью, при контакте с кузовом соли, агрессивная среда начинает разрушать любую защиту покрытия кузова;
- Качество кузова. Скорость коррозии зависит от наличия в металле специальных добавок. Так, например, если взять бюджетные машины двадцатилетней давности, то в настоящее время не найдется ни одной, кузов которой сохранился на сегодняшний день без следов коррозии, в отличие от дорогих марок того времени, при производстве которых кузов был сделан из металла, легированного специальными добавками;
- Влажный климат. В регионах где повышенная влажность, особенно на побережьях около морей, коррозия происходит намного быстрее, так как частички воды при контакте с металлом окисляют его, больше чем воздух.
- Резкие перепады температуры. В зимнее время, при заезде автомобиля с мороза в теплый гараж, на кузове начинает образовываться конденсат, создавая тем самым условия для ржавления металла.
Процесс обработки авто от коррозии
Непосредственно перед самой обработкой кузова автомобиля от коррозии, в первую очередь следует удалить ржавчину. Ржавчина удаляется механически, с помощью специальных приспособлений, таких как: наждачная бумага, болгаркой с наждачным кругом или с помощью пескоструя, последний способ является наиболее эффективным. Для ускорения процесса очистки от ржавчины можно применять специальные растворы, такие как соляная кислота. Самым действенным способом при борьбе с коррозией является использование преобразователей или модификатором. При его нанесении на ржавчину, происходит химическая реакция, при которой оксид железа (ржавчина) преобразуется в таннат железа. Для обработки кузова не нужно иметь специальных навыков, достаточно просто соблюдать следующую последовательность:
- Самым первым делом следует обезжирить поверхность, так как если обрабатывать грязную поверхность антикоррозионными веществами, то толку в их нанесении попросту не будет, для обезжиривания отлично может подойти спирт или растворитель для краски – уайт-спирит.
- Способ, которым вы будете заниматься обработкой кузова от коррозии, зависит от размеров ржавчины. Если ржавчина не значительная, то для удаления достаточно использовать наждачную бумагу. Если коррозия разрослась вглубь металла и по сторонам, то удаления потребуется применить щетку с металлическими зубьями или болгарку с абразивным кругом. Для лучшего эффекта во время удаления рекомендуется использовать специальные растворы ортофосфорной или соляной кислоты, которые своей агрессивной средой смягчают ржавчину, и ее становится проще удалять.
ВАЖНО! После удаления ржавчины с помощью применения растворов, обязательно следует обработать места контакта химии с металлом, так как остатки того или иного вещества провоцируют развитие новых ржавчин.
- В конечном процессе избавления от коррозии, зачищенные части кузова подлежат грунтовке. Следует соблюдать очередность, в первую очередь наносится эпоксидный грунт, а поверх его - акриловый.
Антикоррозийные средства
В настоящий момент имеется большой выбор антикоррозионных средств, которыми можно защитить кузов от ржавления, каждые из которых имеют свои достоинства и недостатки. Автомобильные магазины могут предоставить на ваш выбор следующие средства:
- Парафиновые составы. Имеют преимущества в том, что высыхают сразу после нанесения, образуя эластичный защитный слой, который может сохранять свои свойства при перепадах температуры;
- Битумная мастика. Включает в свой состав синтетические и битумные смолы, которые защищают корпус посредством консервации металла;
- Масляные антикоррозионные средства. Применяются в жидком состоянии, благодаря чему полностью заполняют различные трещины своим составом;
- Поливинилхлоридные материалы из каучука. В основном применяются самими фирмами-изготовителями, так как являются надежными и долговечными;
- Жидкий пластик. Применяется в основном в качестве дополнительной защиты, из-за низкой механической устойчивости.
Данный метод является чисто механическим способом защиты кузова от ржавчины, существует еще один способ, так называемый пассивный метод защиты металлического корпуса благодаря его оцинковке, которую можно так же провести в домашних условиях с помощью специальных средств и прибора. Последовательность обработки следующая:
- Удаляется ржавчина наждачными материалами, насколько это возможно;
- автомобиль ставится на ручной тормоз и запускается двигатель. Привод, входящий в комплект специального прибора, соединяется с плюсовой клеммой аккумулятора. Процедуру, возможно, проводить и при выключенном двигателе, однако это не так эффективно;
- второй конец провода подключается к красному электроду. Для создания гальванического эффекта, корпус машины должен быть заземлен;
- на конце электрода есть губка, предназначенная для впитывания влаги, ее нужно окунуть в раствор для удаления ржавчины, а затем тщательно растереть состав по пораженной области;
- после удаления следов коррозии необходимо смыть остатки раствора водой;
- следующим этапом будет отсоединение красного электрода и подсоединение серого;
- окунуть губку серого электрода в раствор цинка и снова обработать поверхность до тех пор, пока не будет достаточного слоя цинка на ней.
Практика показывает, что оцинковывание двигателя является наиболее действенным методом по борьбе и предотвращению коррозии.
Защита от коррозии двигателя и системы выпуска
Детали внутри автомобиля также уязвимы к появлению коррозии. Система горения топлива и выпуска газов работает в агрессивных условиях. С одной стороны они подвергается высокой температуре, парам кислот и конденсата влаги, а с другой – водой, камнями, солью и грязью. Коррозия, скрытых от глаз мест, возникает вследствие образования во время сгорания топливной смеси – воды, окислов углерода, азота и серы. По своим химическим характеристикам эти вещества являются сильными окислителями металл. В самом глушителе при постоянном образовании нагара и перепадов температур металл особо подвержен к нагрузкам и легко коррозирует. Для защиты внутренних частей автомобиля от ржавления не подойдут средства, которые применяются для защиты кузова, так как температура отработанных газов обычно находится в переделах 400 градусов, а температура металла выхлопной трубы при работе может разогреваться до 300 градусов. Следовательно, для защиты от коррозии нужно использовать только термостойкие эмали и лаки.
СПРАВКА! Для повышения термостойкости эмалей и лаков к ним добавляется алюминиевая пудра.
Помимо выдерживания температуры, специальные вещества должны обладать так же хорошей адгезией, соле- и влагостойкостью. Элементы конструкции окрашиваются защитными веществами с помощью пневматического распыления. Поверхность двигателя в процессе эксплуатации может нагреваться до больших температур. Основными причинами коррозии двигателя являются: масла, пыль и сажа, которые скапливаются на различных узлах деталей, создавая прочную плёнку. Перед антикоррозионной обработкой двигатель следует очистить от грязи и следов масла. Материалы для обработки двигателя от коррозии созданы на основе продуктов нефтепереработки. В их состав входят также ингибиторы коррозии, поверхностно-активные вещества, связующие и наполнители. Средства для обработки деталей обладают хорошей смачивающей способностью и легко проникают в узкие места, пропитывая их и замедляя процесс ржавления. Что касается обработки днища автомобиля, то вещества для защиты от ржавления должны обладать в первую очередь стойкостью к воздействию влаги и большой вибрации.
Каждый автовладелец должен знать, что риск коррозии всегда существует, стоит сказать, что при сборке машин на конвейере их корпус уже на том этапе начинает подвергаться процессам окисления металла. Следовательно всегда нужно уделять должное внимание состоянию кузова и при возникновении малейших дефектов связанных с коррозией применять соответствующие меры.
Чем обработать глушитель от коррозии
Глушитель автомобиля, ровно как и резонатор, а также другие компоненты выхлопной системы, подвержены воздействию агрессивных сред. Это все серьезно влияет на их срок службы, поэтому возникает вполне резонный вопрос: как защитить глушитель и можно ли красить глушитель? Есть варианты глушителей, которые имеют уже защитное покрытие в виде слоя алюминия или слоя цинка, не говоря о дорогостоящих запчастях из нержавеющей стали. На них наносить краску смысла особенного нет, а вот защитить детали из обычной черной стали, вполне возможно.
Среди агрессивных воздействий, самое сильное оказывают:
- перепады температуры, особенно в зимнее время;
- перепады влажности и наличие влаги в выхлопе;
- соли и реагенты, обеспечивающие таяние льда и снега на дорогах зимой, они разрушают детали выхлопа авто;
- небольшие механические повреждения (от небольших камней, мусора и т.д.);
Если покрасить глушитель авто от этих факторов, можно защитить на время выхлопную систему.
Как защитить глушитель от коррозии?
Чтобы получить более-менее эффективный вариант защиты выхлопа, следует верно определить, чем покрасить глушитель автомобиля. Для этого следует взять качественную жаростойкую краску. Температура глушителя может оказаться больше 100 С, а коллектора и все 600-700С, если покрывать краской не только глушитель, то это надо учесть! Кстати, именно такой краской красят глушители на некоторых заводах изготовителях.
Какую краску взять, выбор остается за вами, так как чем покрасить автомобильный глушитель, есть множество вариантов на рынке и множество производителей.
И так, перед тем как красить глушитель следует:
- тщательно зачистить поверхность глушителя, можно «пескоструйкой»;
- глушитель обработать преобразователем ржавчины;
- смыть преобразователь ржавчины водой или тщательно удалить ее ветошью;
- обезжирить растворителем (важный момент);
- загрунтовать;
- покрасить глушитель, при этом наносить жаростойкую краску, желательно из пульверизатора, чтобы минимизировать подтеки.
Если пульверизатора у вас нет, то можно красить глушитель и обычной кистью, если делать это аккуратно.
Нужно ли красить глушитель?
На заводах изготовителях краской красят глушители, чтобы придать им товарный вид, и чтобы до момента продажи они выглядели презентабельно. Как только глушитель устанавливается, то его поверхности попадают под действие агрессивных условий и слой краски довольно быстро исчезает. Следует также учесть, что при установке слой краски страдает от небольших царапин или сварочных работ, что фактически сводит на нет такую защиту.
Внутренняя часть глушителя не имеет покрытия краской и получает воздействие коррозии и температуры напрямую, поэтому защита только наружных поверхностей краской не выглядит слишком эффективной.
Не смотря на все это слой краски, правильно наложенный на внешнюю поверхность глушителя, все же защищает его какое-то время, и эта защита вполне может несколько увеличить время работы детали.
Красить глушитель или нет, решать только вам. Если вы хотите, чтобы глушитель или любой другой компонент выхлопной системы автомобиля служил вам долго, то выбирайте качественные детали тех производителей, которым доверяете.
- Защита глушителя своими руками
- Зачем нужна защита глушителя?
- Как произвести защиту глушителя?
- Как максимально продлить жизнь глушителя?
Выхлопная система является одним из компонентов транспортного средства, которому автолюбители уделяют меньше всего внимания. Обычно думать о глушителе начинают, когда звук становится «спортивным», а автомобиль начинает походить на турецкий барабан или табун лошадей. Когда звуки начинают достигать уровней Формулы-1, мы бежим в магазин запасных частей и судорожно ищем свободный автосервис.
На практике выхлопная система является одной из самых активных в транспортном средстве, работающих в экстремальных условиях — высокой амплитуды температур, сильной вибрации, внутренней и внешней коррозии, а также подвергается атаке камней, грязи, воды и щёлочи в зимний период. В данном материале мы расскажем о том, как надёжно защитить глушитель от воздействия данных факторов.
Зачем нужна защита глушителя?
В современных автомобилях глушитель не просто «горшок», а выполняет ряд важных функций:
1. Минимизирует шум двигателя;
2. Снижает уровни вредного оксида углерода, окислов азота и не сгоревших углеводородов;
3. Направляет выхлопные газы, минуя пассажирский салон;
4. Оптимизирует работу двигателя путём обеспечения непрерывного и равномерного потока выхлопных газов из двигателя.
Повреждение системы, помимо раздражающих звуковых эффектов, представляет реальную опасность проникновения в салон ядовитых газов, которые могут серьёзно повредить здоровье водителя и пассажиров. Неисправность выхлопной системы может привести к снижению мощности двигателя и динамических характеристик автомобиля. Для обеспечения надлежащего функционирования, выхлопная система должна регулярно проверяться. Если этого не сделать, имеется риск повреждения в самый неожиданный момент. Дело в том, что повреждение выхлопной системы является одной из 10 причин, по которой требуется вызывать эвакуатор.
Как произвести защиту глушителя?
Учитывая обилие гравия на наших дорогах, повредить защитное покрытие глушителя очень просто. После этого в месте повреждения начинает образовываться ржавчина, а соль, которой щедро усыпаны наши дороги зимой, только ускоряет этот процесс, что впоследствии приведет к ремонту, сварке, а то и замене самого глушителя. Чтобы этого всего избежать, достаточно хотя бы раз в год осматривать всю выхлопную систему. Если при осмотре вами были обнаружены очаги ржавчины, лучше долго не затягивать с ремонтом. Стальная защита выхлопной системы обеспечивает следующее:
Повышенная жёсткость защиты обеспечивается за счет использования горячекатаной стали и штампованных элементов.
• Безопасность защиты – это согласованность с пассивными средствами безопасности автомобиля, при лобовом столкновении защита не мешает двигателю смещаться вниз.
• Самостоятельная установка возможна, так как защита устанавливается в штатные отверстия автомобиля и имеет в комплекте крепежные элементы.
• Стальная защита прослужит долго, в силу того, что обрабатывается специальными антикоррозийными средствами, а для монтажа используется оцинкованный крепеж.
Порядок установки на автомобиль:
1. Установить на трубу глушителя перед кронштейном.
2. Установить на трубу глушителя за кронштейном.
3. Установить на ранее закрепленные скобы щит.
Чтобы как-то защитить глушитель от коррозии, используют различные методы. К примеру, в США и в некоторых других странах 90% глушителей создают из алюминированной стали. На поверхность такой стали диффузионным способом наносится смесь порошков оксидов алюминия и алюминия. Долговечность глушителя при всем этом растет раза в два-три. В Англии для производства глушителей берут сталь, в которой содержится 36% титана и 11% хрома. Еще для производства глушителей идет сталь, легированная молибденом.
Более качественно защищает внешние поверхности системы выпуска от коррозии их расцветка. Но, окрашивая поверхности системы, необходимо принимать во внимание, что температура отработавших газов у выпускного трубопровода колеблется от 420°С до 760°С, тогда как температура металла выхлопной трубы колеблется от 200°С до 540°С. Окрашивать систему выпуска следует только теплостойкими лаками и эмалями. Термостойкость лака можно прирастить добавлением 6-10% дюралевой пудры. Пудра добавляется в лак только перед его применением, так как пудра при продолжительном хранении (больше 4 часов) начинает терять свою способность всплывать, из-за чего ухудшается внешний облик покрытий и эксплуатационные характеристики.
Также есть и другие способы защиты системы выпуска от коррозии, которыми пользуются и автовладельцы, и мастера. К примеру, такой — поверхность глушителя и выпускной трубы очищается от рыхловатой ржавчины и грязевых отложений, потом покрывается графитовой смазкой (наносить необходимо узким слоем). После того как смазка обгорит, она оставит после себя крепкую антикоррозионную пленку темного цвета, которая и защитит детали от коррозии.
Как максимально продлить жизнь глушителя?
1. Избегайте поездок на короткие расстояния — при низкой температуре возникает конденсация водяных паров на внутренних компонентах системы. Вода, взаимодействуя с некоторыми соединениями, присутствующими в выхлопных газах, образует кислоты, и, в свою очередь, вызывают сильную коррозию, значительно уменьшая срок службы системы.
2. Избегайте езды в сложных дорожных условиях — песок, грязь, камни, солёная вода на поверхности дороги, всё это может привести к повреждению выхлопной системы. Если горячие элементы системы попадают в воду или касаются снега, возникает быстрая усадка, ослабевают сварные швы и уплотнения компонентов.
3. При ремонте выбирайте качественные запасные части и квалифицированный сервис. Это будет гарантией того, что выхлопная система прослужит долго, позволит избежать дефектов при эксплуатации, а установка будет выполнена правильно, правильными инструментами с соблюдением требуемых расстояний до кузова и элементов подвески.
Подписывайтесь на наши ленты в таких социальных сетях как, Facebook, Вконтакте, Instagram, Twitter и Telegram: все самые интересные автомобильные события собранные в одном месте.
Читайте также: