Какие двигатели ставят на камаз мастер
Как строит двигатели «КАМАЗ-мастер»: 1150 лошадиных сил из обычного мотора
На мировых ралли-марафонах гоночная команда «КАМАЗ-мастер» непобедима уже несколько десятков лет. Залог триумфа — невероятный труд всего состава команды: от рядовых механиков до пилотов-чемпионов. Однако не стоит забывать и про технику, которую создают отечественные инженеры и благодаря которой российские грузовики КАМАЗ знает весь мир. Корреспондент журнала «Движок» побывал в цехах самой титулованной гоночной команды России и своими глазами увидел, как создаются непобедимые грузовые болиды.
Гоночные соревнования мирового уровня — это не только накал спортивной борьбы, но еще и изрядная доля всевозможных закулисных интриг, внутренних организационных нюансов и финансовых перипетий. Мировые ралли-марафоны тут, увы, не исключение. За время проведения разных соревнований неоднократно всплывали всевозможные истории о том, что организаторы, как сейчас модно говорить, «хайли лайкли» — не всегда объективны и беспристрастны по отношению к разным участникам и командам.
Как ни крути, но «КАМАЗ-мастер» с этой точки зрения давно в перекрестии прицела, причиной чего являются, конечно, безостановочные победы. Ни организаторам гонок, ни другим участникам не особо интересно, когда победитель на 90% известен заранее, а оставшиеся 10% приходится списывать фактически только на отвернувшуюся от россиян удачу.
Гоночные чиновники с завидной регулярностью ужесточают технический регламент и с особой скрупулезностью занимаются проверками — конечно же, в первую очередь тех, кто претендует на победу. Официальное объяснение такого подхода — борьба за равные условия участия, нормы безопасности и, в последнее время, экологические тренды. Реальное положение дел часто намекает на то, что технические требования — возможность выбить из борьбы «не тех» лидеров.
В прямом разговоре камазовцы «теорию заговора» отвергают, однако, не скрывая, говорят о том, что судьи международных соревнований нередко применяют максимальные наказания к «КАМАЗ-мастер» за то, за что другим участникам гонки порой просто прощают.
Именно по этой причине быть начеку приходится не только «боевым» экипажам, но и инженерам, которые создают гоночный грузовик. Малейшее отступление от техрегламента может дорогого стоить.
Собственно, одним из камней преткновения всегда был двигатель. «КАМАЗ-мастер» прекрасно сражался с отечественными моторами — до 2010 года на гоночных грузовиках стоял 18,5-литровый агрегат V8 ЯМЗ, а после команда перешла на простой и надежный мотор ТМЗ мощностью 850 л. с. Кстати, его же первоначально использовали как основу для гибридного газодизельного грузовика Сергея Куприянова.
Часто обыватель задается вопросом, почему такой гигант, как КАМАЗ, не может сам сделать двигатель? Главная причина заключается в том, что по правилам гонок двигатель должен быть серийным. То есть сделать мотор мало — его еще нужно запустить в массовое производство для гражданских грузовиков, что стоит колоссальных затрат и усилий. А с учетом того, что требования организаторов соревнований за 10 лет поменялись четыре раза (!), данная затея становится бессмысленной
Итак, новым мотором стал серийный Cummins ISZ-13, выпускаемый по лицензии в Китае компанией Dongfeng. Это рядный шестицилиндровый двигатель объемом 13 литров и мощностью 450 л. с. Агрегат оказался по габаритам выше и короче прошлых V-образных «восьмерок», а потому с учетом новых габаритов машину фактически пришлось проектировать заново.
Двигатель в первую очередь устраивал команду по надежности, а вот его серийные характеристики по мощности и тяге нужно было увеличивать минимум вдвое, доводя до гоночных показателей.
Первым делом двигатель разбирается, после чего каждая деталь подвергается ревизии. Блок, цилиндры, клапаны, распредвалы, система впрыска и выпуска, охлаждения и турбонаддува — все это проходит проверку на возможность улучшения характеристик мотора. Более того, улучшенные, а чаще всего полностью замененные детали должны еще надежно работать друг с другом, что требует целой серии испытаний. На стеллажах производства «КАМАЗ-мастер» лежат десятки различных видов компонентов, которые подбираются к новому мотору, а иногда создаются под заказ.
Отдельный цикл работ ведется по подбору характеристик турбокомпрессора и оптимизации программы управления двигателем. Далее мастера вручную собирают мотор, подбирают смазочные материалы и на финальном этапе отправляют получившийся агрегат на испытательный стенд, где двигатель работает по специальной программе фактически на предельных нагрузках.
В результате от серийного мотора Cummins ISZ-13, по сути, родным остается только корпус и шорт-блок, а характеристики достигают впечатляющих показателей: 1150 л. с. и 5000 Нм крутящего момента. С такими данными гоночный КАМАЗ разменивает первую «сотню» за 6 секунд.
Само собой, на моторе испытания не заканчиваются. Все остальные агрегаты также подвергаются существенным изменениям. Так, например, форсированный двигатель повысил температуру выхлопа с 800 до 900 °C, что потребовало применения дорогих более жаростойких материалов. И так практически по каждой системе.
Применение иностранных комплектующих в отечественных гоночных машинах — мировая практика. Глобализация чисто экономически не позволяет каждому производителю быть полностью автономными в постройке машин. Куда больше смущает ситуация в российском производстве: в цехах КАМАЗ-мастер, как и много где, отечественного оборудования почти не найти. Особенно «прекрасно» выглядит рабочее место на пильном станке, оператор которого, создавая детали для гордости российского автоспорта, всю смену смотрит. на американский флаг. Увы, производство средств производства в России было почти полностью уничтожено в ходе перестроечных реформ.
Каков итог?
Камазовцы открыто говорят о том, что гоночный КАМАЗ построен с массовым применением импортных комплектующих. Многие детали освоены на российском производстве и дают рабочие места в нашей стране — та же кабина К5 локализована на 100% и скоро появится на гоночных грузовиках.
А самое главное, закупка импортных агрегатов при отсутствии затрат на разработку оставляет огромный потенциал для развития нашей инженерии при минимальных вложениях. Тот же двигатель Cummins ISZ-13 от грузовика Dongfeng и от гоночного КАМАЗа 43509 — по факту два разных мотора. В последний вложено столько отечественных идей, что агрегат можно смело называть российским.
Собственно, и правда: подобным путем отечественный автопром шел с момента своего основания, когда еще в царской России в 1908 году было освоено производство бельгийских автомобилей Fondu. А после уже советская власть локализовала у нас модельный ряд Ford, превратившийся в «эмки» и «полуторки», на которых была выиграна война. Про итальянские «Жигули» тоже знают все. Вопрос исключительно в конечном результате. А в случае с «КАМАЗ-мастер» он остается неизменным: какие бы условия ни выставлял технический регламент FIA, на каком бы континенте ни проходил очередной «Дакар» и какие бы агрегаты ни использовал отечественный автогигант, золото соревнований остается в России.
Mike-fiesta › Блог › Двигатели для гоночных КАМАЗов, некоторые подробности
Как-то в одном из постов я пообещал вам показать новый двигатель, который стали устанавливать на гоночные КАМАЗы. Одно время эти снимки нельзя было демонстрировать, а потом добро дали, да я забыл уже про них, сегодня исправляюсь.
Все уже знают наверняка историю, что требования по объёму двигателей для "дакаровских" гоночных грузовиков постоянно менялись и было принято решение ограничить их на уровне 13 литров (сейчас пока можно применять 16-литровые). "КАМАЗ-мастер" стал испытывать несколько разных вариантов двигателей с такими объёмами, и остановился в итоге на 13-литровых американских моторах Cummins QSZ13, собираемых по лицензии… в Китае. Когда мы были на базе команды в декабре 2016-го, то как раз застали момент, когда на моторном стенде испытывали такой агрегат.
Данный стенд позволяет моделировать самые разнообразные режимы работы, в том числе имитирующие реальную эксплуатацию, задавать повышенные нагрузки и т.п. Так вот, испытателям понравилось, как вёл себя "базовый" двигатель Cummins QSZ13 в сложных режимах. И было решено заняться его форсировкой, и затем испытать в гоночных условиях. Мой коллега avalanche уже этой осенью побывал на базе и выяснил, что пока такой стоит только на машине экипажа Дмитрия Сотникова. Остальные продолжают использовать 16-литровые Liebherr, которые вскоре окажутся вне закона.
Краткое напоминание вопроса для тех, кто пропустил. Напомню, в 2012-м на топовых грузовиках "КАМАЗ-мастера" в последний раз использовался двигатель V8 ТМЗ-7Э846.10 (Тутаевского моторного завода), рабочим объёмом 18,5 литров, мощностью 850 л.с. и с крутящим моментом 2700 Нм, при снаряжённой массе грузовика в 9300 кг. Двигатель команде нравился, надёжный был, хоть и устаревший.
С 2013 года техтребования изменились. Максимальный рабочий объём не должен был превышать 18 литров. Тогда был найден вариант с швейцарско-немецким тракторным силовым агрегатом Liebherr D9508 V8. Причём его доводку до гоночных кондиций осуществляли непосредственно в Набережных Челнах, на базе команды. В итоге официальные характеристики КАМАЗа 4326 с ним таковы: рабочий объём 16 литра, мощность 920 л.с., крутящий момент 4000 Нм, при снаряжённой массе машины 8900 кг.
Хотя, по признанию сотрудников коллектива, с "Либхерром" им пришлось помучаться, и вначале его надёжность не устраивала, но потом смогли довести до нужных кондиций. И вновь коллектив из Татарстана стал побеждать, хотя сделать это становилось всё сложнее, менялся и характер трассы в "Дакаре", в сторону упрощения. В 2016-м первое место было упущено, но уже в 2017 челнинцы смогли вернуться на вершину, и снова победить !
«КАМАЗ-мастер» в мире моторов
«Дакар-2018» – последний, в котором в грузовой категории позволяется использовать моторы объёмом более 13 литров. Для большинства команд это мало что меняет, так как большая часть грузовиков и без того на протяжении многих лет оснащались моторами меньшего объёма. Но для «КАМАЗ-мастер» это изменение знаковое – ведь основным мотором для команды последние годы был двигатель Liebherr V8 объёмом 16 литров.
Именно такие двигатели стоят на трёх из четырёх КАМАЗах на нынешнем «Дакаре». На четвёртом, под управлением Дмитрия Сотникова, установлен экспериментальный 13-литровый мотор, рядная «шестёрка», который и должен стать той силовой установкой, которая будет устанавливаться на КАМАЗы в будущем.
Смена мотора для «КАМАЗ-мастер» далеко не новость. За годы выступлений на ралли-рейдах команда использовала силовые установки самых разных компаний (КАМАЗ, Cummins, ЯМЗ, ТМЗ, Liebherr), самых разных конфигураций (рядные «шестёрки», V8 и даже V12) и самых разных объёмов (от 11 до 25 литров). О том, почему «КАМАЗ-мастер» использовал такие большие двигатели, и почему остальные команды предпочитали моторы гораздо меньших размеров, нам рассказал технический директор команды Владимир Губа.
Владимир Губа: Причина использования большинством команд 13-литровых моторов проста: все ведущие команды в мире ралли-рейдов ставят на свои грузовики моторы, которые используются в кольцевых гонках, в чемпионате Европы по гонкам грузовиков. На кольцевых грузовиках строгий регламент — двигатель 13 литров, 10 цилиндров, одноступенчатый наддув. Это достаточно совершенные двигатели, разработанные специально для гонок. Там есть команды MAN, Iveco, Mercedes. Команда Tatra в ралли-рейдах ставит на свои грузовики тот же двигатель, который используется на кольцевых грузовиках команды Buggyra. Поэтому в этом плане им несколько проще. Они берут двигатель мощностью 1200 лошадиных сил и моментом в 6000 Н*м, и дефорсируют его до уровня 1000 лошадиных сил, и 4500 Н*м.
Но это специальный продукт. Мы не можем так поступать, у нас нет своей команды в гонках грузовиков. Мы пробовали работать с мотором Buggyra, но строить на его базе грузовики мы не можем, потому что мы профессиональная команда, и наше преимущество в том, что мы досконально знаем все компоненты нашего автомобиля. Мы должны иметь возможность их диагностировать, проверить, отремонтировать в любых условиях. Если мы берем готовый узел, то, как правило, не знаем, что у него внутри, не имеем доступа к программе, не имеем даже доступа к диагностике. То есть мы целиком и полностью завязаны на услугах поставщика. Нам это не подходит.
Поэтому мы действуем обратным образом – берём за основу серийный двигатель. Так было и в случае с Liebherr — мы взяли серийный двигатель, который применялся на спецтехнике, а отдельная модификация использовалась на грузовиках MAN. Но это серийный двигатель мощностью 500 киловатт, 700 лошадиных сил. Мы его форсировали, довели мощность до 1000 лошадиных сил. Сейчас то же самое делаем с 13-литровым двигателем Cummins. Мы взяли двигатель мощностью 520 лошадиных сил, и стараемся добиться от него мощности более 1000 лошадиных сил, увеличиваем момент в два раза.
Моторы Cummins ставятся и на серийные КАМАЗы, но маленькие, 7-литровые. Недавно запустили производство 9-литровых. То есть, с точки зрения объёма они пока занимают низшую ступеньку в иерархии этих силовых установок. Мы же используем 13-литровый двигатель. Это не первый наш опыт работы с Cummins, они стояли на наших грузовиках, в том числе гоночных, еще в 90-е годы. А уже в 2007-2008 году использовали 15-литровый двигатель Cummins, с двойным турбонаддувом. Он себя не очень хорошо показал, что лишний раз подтверждает неэффективность работы с чужим мотором. Он был сделан по заказу, и, естественно, производитель закладывает определенный резерв для клиентского двигателя, чтобы, не дай бог, чего не случилось. Поэтому характеристики его оказались не лучшими. Тем не менее, мы сейчас опять вернулись к блоку цилиндров Cummins. Но уже разрабатываем всё сами, и стремимся подойти к пределу его возможностей.
Сейчас мы работаем с Cummins на таких условиях: мы покупаем у них двигатели специальной комплектации, они оказывают нам помощь запасными частями и некоторой информацией. Но все разработки, все изменения, все доводки, все испытания мы ведём сами. Почему Cummins? Такой выбор сделан по той простой причине, что по регламенту эти двигатели должны производиться серийно и устанавливаться на коммерческие грузовики. Пока такого мотора у КАМАЗа нет, а ждать, когда он появится, и начинать работу только после этого – это потеря времени. Наш Научно-технический центр (НТЦ) сейчас как раз работает над версией 13-литрового двигателя с очень близкими показателями. Мы же работаем на опережение, и к тому моменту, когда начнётся его серийное производство, мы уже будем готовы. Думаю, мы достаточно быстро сможем перенести весь опыт на свои отечественные двигатели, и уже тогда начнём ездить на своих двигателях.
Несмотря на то, что на наших машинах и на грузовиках наших конкурентов стояли моторы очень разных размеров, мощность у них была примерно одинаковая. Почему? Помимо прочего, она ограничена разумными рамками. Максимальная скорость на ралли-рейдах сейчас ограничена регламентом на уровне 140 км/час. Для такой скорости, в общем-то, 1000 лошадиных сил вполне достаточно. Излишняя мощность — это нагрузка на трансмиссию, это более сложные режимы работы, температура, давление и так далее.
Действительно, долгие годы «КАМАЗ-мастер» использовал двигатель большого объема, 18,5 литра. Мы даже как-то пробовали ярославский 24-литровый 12-тицилиндровый мотор. Но от него быстро отказались, потому что он всё ломает. Избыточная мощность. Так что вернулись к 18,5-литровому, ярославскому, или сейчас тутаевскому двигателю. Но это мотор достаточно старой разработки.
Он неплохой по конструкции, но цельноалюминиевый. Главное – у него алюминиевые головки. И они не позволяют выходить на высокие степени форсировки. У всех современных моторов уже чугунные головки. Поэтому для того чтобы обеспечить такую же мощность, степень форсировки была гораздо ниже – с алюминиевой головкой невозможно достичь тех же давлений, тех же температур. Поэтому на выходе мы получали такие же показатели, но с более низкими удельными показателями. С меньшей теплонапряженностью. С меньшей нагрузкой на механические узлы и детали.
Но затем максимальный разрешённый рабочий объём двигателей уменьшили, и последние пару лет на грузовиках стоят 16-литровые двигатели Liebherr. Он имеет примерно такие же параметры, как и ярославские моторы. Мы пытались выйти на более высокие показатели в мощности, но есть у V-образных двигателей одна особенность — у них два шатуна находятся на одной шатунной шейке. И ширина вкладышей достаточно маленькая, это самое напряженное место. То есть, мы достигаем определенного момента – и всё. Да, теоретически турбонаддув и система топливоподачи позволяют выйти на больший момент, на большую мощность. Но механически увеличивать её уже больше невозможно. Потому что вкладыши, даже самые лучшие, не выдерживают. За счёт меньшего уровня форсировки была повышена надежность, увеличен ресурс этих двигателей.
Сейчас мы переходим на рядный 6-цилиндровый двигатель, там нет этого ограничения. Но есть другие, связанные, например, с более высокой тепловой напряженностью. Если у наших «восьмерок», больших двигателей, температура выхлопа была около 800 градусов, то сейчас повысилась до 900 градусов. Это уже существенно. То есть, такие моторы требуют другого подхода, использование других, более дорогих материалов.
Конечно, у двигателя меньшего размера есть свои плюсы. С точки зрения массы, 13-литровый двигатель легче процентов на 25. Но, с другой стороны, рядный мотор длиннее и выше. То есть V-образный двигатель примерно на два цилиндра короче, и за счёт развала он ниже, поэтому под новый мотор нам пришлось проектировать практически с нуля весь автомобиль. Изменено положение двигателя, расположение по высоте, по длине. Изменилось положение кабины, потому что прежнее, над двигателем, мы использовать уже не могли – кабина слишком высоко поднимается. Поэтому мы искали новые варианты, чтобы максимально эффективно разместить массы, не увеличивая высоту центра тяжести. Так что, как обычно в спорте, нет какой-то концепции, позволяющей всегда побеждать – всё упирается в поиск компромиссов.
Основные силовые установки гоночных грузовиков «КАМАЗ-мастер»
* – грузовик капотной компоновки, на ралли-рейдах «Дакар» не использовался
Гроза «Дакара». Как устроен гоночный грузовик «КАМАЗ»?
Жара под 40 градусов, солнце беспощадно разогревает песок и всё вокруг, где-то вдалеке нарастает гул, который по мере приближения начинает сопровождаться треском веток и всё более выраженным рокотом могучего двигателя. Проходит несколько секунд, и появляется грузовик, выскакивая из поворота с эффектным заносом. Разгон, гудок, трамплин — десятитонный «КАМАЗ» пролетает в воздухе несколько метров и уносится дальше, поднимая клубы пыли. И это не марафон «Дакар», а полигон в окрестностях Набережных Челнов!
Как всё начиналось?
Удивительно, но мы впервые оказались не только на полигоне, но и на базе команды «КАМАЗ-мастер», которая при поддержке завода и партнёров уже больше 30 лет готовит гоночные грузовики — официальной датой создания считается 17 июля 1988 года. В первых ралли-рейдах челнинцы использовали практически серийный трёхосный «КАМАЗ-4310», но главные успехи пришли к ним позже — к середине 90-х стало понятно, что за победы могут бороться только спортпрототипы, лишь отдалённо похожие на дорожные машины.
В 1994-м появился «КАМАЗ-49252» — тот самый двухосник с характерным окрасом и скошенной платформой. Могучий дизель ЯМЗ был расположен в пределах колёсной базы и при объёме 17 литров выдавал 750 «лошадей» и разгонял машины вплоть до 180 км/ч! А первые победные «Золотые бедуины», главные призы за победу в марафоне «Дакар» приехали в Набережные Челны в 1996-м, долгожданный триумф принёс экипаж Виктора Московских.
С тех пор синие двухосные «КАМАЗы» не покидают число лидеров «Дакара» — с 2000 по 2011 годы Владимир Чагин побеждал в легендарной гонке рекордные (в грузовой категории) семь раз! Соперники прозвали его «Царь Дакара». В 2012 году Чагин занял пост руководителя команды, но смену вырастили достойную: из десяти последних «Дакаров» было выиграно восемь!
Как стать пилотом гоночного грузовика?
Путь за руль такого «КАМАЗа» отличается от более привычных дисциплин автоспорта — грузовик стоит дорого (заводчане не раскрывают точных цифр, но это явно десятки миллионов рублей), и в аренду его взять негде, как, например, легковую машину для ралли или кольцевых гонок. Поэтому всё начинается ещё в далёком детстве с. картинга!
Да, оказывается, «КАМАЗ-мастер» имеет программы поддержки картинга и багги, затем молодые ребята присоединяются к команде на различных тренировочных сборах и тестах, впитывая знания и опыт. Если кандидат подходящий, то следующим этапом становится кресло механика — в грузовых экипажах ездят по 3 человека. И только потом, если в руководстве сочтут, что «пора», то попадёшь за руль. Поэтому все гонщики достаточно взрослые — самому молодому, Айрату Мардееву, в этом году исполнилось 33.
Именно такие этапы прошёл Эдуард Николаев — родился в Набережных Челнах, занимался картингом, а в 2010 году в возрасте 25 лет стал победителем «Дакара», будучи механиком как раз в экипаже Владимира Чагина. Спустя три года он повторил успех уже за рулём «КАМАЗа», а в дальнейшем выиграл ещё три раза подряд (с 2017 по 2019). Так что до рекорда Чагина Николаеву осталось всего два «Золотых бедуина».
Как устроен гоночный «КАМАЗ»?
Технический регламент «Дакара» часто меняется, иногда даже в самый неподходящий момент — организаторы марафона не любят доминирования одной команды, но «КАМАЗ-мастер» каждый раз находит лучшие решения. Например, постоянно уменьшают рабочий объём двигателя, что вынуждает менять партнёра или поставщиков. Когда-то «камазовцы» использовали огромные двигатели ЯМЗ — V8 объёмом до 18 литров и даже 26-литровый V12 (последний не прижился, так как буквально уничтожал трансмиссию), в 2013 году ограничение вынудило перейти на импортный V8 Liebherr, а очередной новый грузовик пришлось создавать к «Дакару» 2019 года.
Синяя армада: как «Камаз» стал единственным русским суперкаром
В автомобильном мире до сих пор не придумано лучшего способа проверки новых технологий и обкатки конструкторских решений, чем автоспорт. Из ралли, «Формулы-1» и кузовных чемпионатов под капоты гражданских автомобилей пришли компрессоры и турбины, непосредственный впрыск и системы рекуперации энергии, оттуда же рядовым водителям достались бесчисленные электронные ассистенты. Но если для производителей легковых машин наличие гоночных команд естественно и понятно, то в мире грузового транспорта все не так очевидно.
«Камазу» повезло — он подхватил автоспортивный «вирус» от своего волжского собрата «Автоваза». Переведенный из Тольятти в Набережные Челны решением министра на должность директора автосборночного завода Михаил Годзинской организовал там секцию ледовых гонок по аналогии с тольяттинской. Она стала очень популярной, и из нее вскоре выросло ежегодное ледовое ралли «Интер-директор» на легковых автомобилях — по сути тимбилдинг для директоров автомобильных заводов СССР и их иностранных партнеров.
На ралли приезжали, как сегодня сказали бы, топ-менеджеры со всей страны, а также поставщики деталей из Европы. Об уровне челнинских любителей автоспорта говорит тот факт, что, когда на заводе открылась еще и секция багги, пять ее членов вскоре вошли в сборную страны, а когда в Москве по аналогии с «Интер-директором» было организовано летнее ралли «Директор», его первым победителем стал руководитель Научно-технического центра «Камаза» Семен Якубов, будущий руководитель команды «Камаз-Мастер» и штурман экипажа Владимира Чагина.
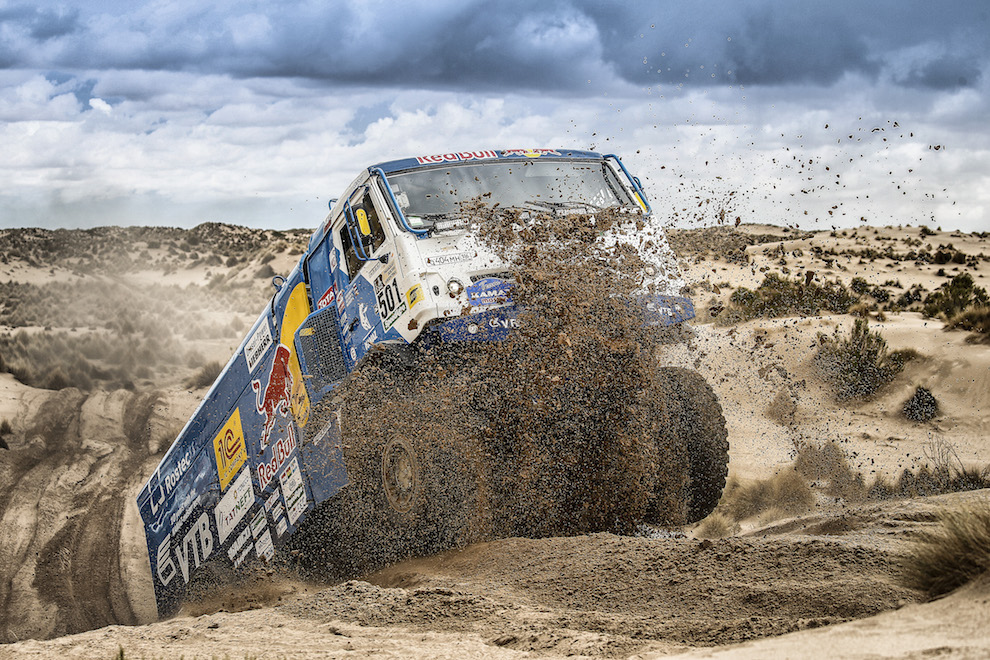
В январе 2018 года команда «Камаз-Мастер» одержала свою 15-ю победу в зачете грузовых автомобилей ралли «Дакар» / DR
«Грузовой спорт тогда уже существовал, и у нас на заводе была команда по кроссу, — вспоминает Якубов, — но после того как один из членов ЦК выступил в газете с критикой, мол, грузовики должны возить грузы, а не гоняться друг за другом, это направление прикрыли, и потом эти грузовики долго стояли в углу двора автосборочного завода. Потом была попытка соревнования в кольцевых гонках. Раскрашенные грузовики, девушки в купальниках — все побуждало к участию, и мы подготовили два автомобиля, но выше пятого места подняться не могли. Знаете, наша автомобильная промышленность не была лучшей в мире. Я понимаю, что не открыл для вас Америку, но мы это на себе почувствовали: двигатели наши были слабые, про электронику мы еще не слышали, у всех инжекторы, а у нас — карбюраторы, дисковые тормоза даже на легковые машины не ставили. Соревноваться было тяжело. И хотя мы завоевывали призы, но только зрительских симпатий, все видели, как мы боролись. Мы проходили повороты в заносе, обходя соперников, но на прямых все равно отставали. И тут я узнал про «Дакар».
Увы, сразу попасть на гонку легенду не удалось. На «Дакаре» 1988 года произошла трагедия: уникальный грузовик DAF Turbo Twin с двумя моторами, каждый из которых управлял отдельной осью, попал в аварию, в которой погиб штурман. Тот DAF по ходу гонки раз гонялся до 200 км/ч и легко обгонял и грузовики, и легковые машины, но трагедия заставила организаторов ввести ограничения: в классе гру зовиков теперь могли участвовать только серийные модели. Так что первые международные старты раллийных «Камазов-4310» состоялись на ралли «Ельч» и ралли «Обжектив Сюд», на каждом из них советские грузовики заняли второе и третье места. В 1990 году с определенными ограничениями разрешили участие грузовиков в «Дакаре».
«Камаз-Мастер» 4326
Классические суперкары способны поражать только на идеальных дорогах, но российский суперкар от «Синей армады» готов лететь не разбирая дороги. Пустыни и скалы, болота и снежные поля — все это для него естественная среда обитания. Вот какие технологии обеспечивают грузовику «Камаз-Мастер» превосходство на любом покрытии.
Двигатель
16-литровый V8 Liebherr D9508, мощностью 950 л. с. с крутящим моментом 4500 Нм. Первое время боевые машины использовали 305-сильные 11-литровые V8 «Камаз-7403», но в пожаре, уничтожившем завод двигателей, погибли и проходившие там подготовку боевые дакаровские агрегаты, поэтому команде пришлось временно перейти на 14-литровые 520-сильные Cummins N14-500E, после чего началась почти 20-летняя эпоха моторов Ярославского и Тутаевского моторных заводов — ЯМЗ и ТМЗ 7Э846/7/8, объемом 18 л, мощностью 850 л. с. и с крутящим моментом 2700 Нм (модификации этих двигателей можно встретить на карьерных самосвалах «Белаз», речных буксирах и локомотивах). Тяжелые и прожорливые, но неубиваемые и всеядные, они легко справлялись с любым топливом и были заменены только после введения на «Дакаре» ограничения на объем. На смену им пришли 13-литровый Cummins ISZ-13 и 16-литровый Liebherr D9508, мощностью 920 и 980 л. с. соответственно. Моторы «Камаз-Мастер» закупает серийные, после чего форсирует и перестраивает моторы в своем Научно-техническом центре. О масштабе доработок гово- рит тот факт, что после них мощность возрастает примерно в два раза.
Масса
10,2 тонны. Для сравнения: первый грузовик весил 10,5 тонны, а был в истории команды и 12-тонный монстр. Чтобы сделать машину легче, идут на всевозможные хитрости — например, обрезают болты, которыми крепятся колеса. Минимально разрешенная по регламенту масса — 8,5 тонны.
Кабина
Замена кабины по ходу гонки запрещена, при этом менять двигатель, оси, трансмиссию и другие ключевые детали можно. На стадии проектировки грузовика размер и расположение кабины зависит от выбранного двигателя. В ближайшее время место немецкого мотора займет камазовский, который сейчас проходит последние испытания.
Радиатор
Январь в Южной Америке более жаркий, чем в Африке. Поэтому система охлаждения была переделана, ведь от температуры масла зависит скорость машины.
Почему "КАМАЗ" выигрывает "Дакар", но не может стать мировым производителем техники?! Рассказываю в чем причина!
Эта мысль мучала меня очень давно. "КАМАЗ" побеждал практически в каждом проводимом "Дакаре" и даже 4 раза за его историю брал все призовые места, что произошло и в 2021-ом году, если вы не в курсе.
Призовые места расположились так:
1. Дмитрий Сотников / Руслан Ахмадеев / Ильгиз Ахметзянов («КАМАЗ-мастер») — 48:21.21
2. Антон Шибалов / Дмитрий Никитин / Иван Татаринов («КАМАЗ-мастер») +41.38
3. Айрат Мардеев / Дмитрий Свистунов / Ахмет Галяутдинов («КАМАЗ-мастер») +1:16.35
Заваривайте чай/кофе, объясню все интересно!
Не путать мясо с рыбой!
Команда "КАМАЗ-Мастер" появилась 17 июля 1988 года. Первым официальным соревнованием было ралли «Ельч» в Польше. На гонку было выставлено три грузовика-внедорожника марки «КАМАЗ», и одному из них удалось получить серебро
Стоит различать обычные "КАМАЗЫ" и те, что учавствуют в "Дакаре", точнее они вообще ничего общего не имеют и даже технологии, используемые в гонках - на конвейер не переходят, а стоило бы!
В самом последнем болиде, который попал под новый технический регламент о снижении литража двигателя до 13л объема - нет практически ни одной отечественной детали.
- Двигатель: DCEC ISZ-13 - собирается в Китае и дорабатывается на американском оборудовании в цехах ТНЦ "КАМАЗ"
- Коробка: ZF Германия
- Амортизаторы: Нидерланды
- Сцепление: Германия
- Тормоза: Бельгия
И только шины "Кама-Евро" на которых выступает "КАМАЗ" - Российские! Гордость взяла, эхх.
Вот что говорят в самом "КАМАЗе":
Что идет на экспорт? И почему "КАМАЗ" им не надо?
Начнем с того, что в Европу "КАМАЗ" по определению попасть не может - спасибо санкциям, но даже если бы их не было, тягач не вписался бы в эконормы.
Рядный 6-цилиндровый двигатель модели КАМАЗ-910.10-550, плод сотрудничества автогиганта с немецкой компанией Liebherr лезет в Евро-5, но до Евро-6, к сожалению, не дотянул, хотя такая возможность есть, вероятно, они доведут его до ума, чтобы заняться экспортом в Европу.
Сам "КАМАЗ" не отрицает, что делает направление в премиум сегмент, но, будем откровенны, цена в 6,5-7 млн рублей, с условием, что Mercedes можно купить за 7+, ну, я не дальнобойщик, конечно и фурой то никогда не рулил, поэтому, ответьте в комментариях, что лучше - "КАМАЗ" или "Мерседес" в виде тягача?
В любом случае, экспорт возможен лишь в страны ближнего зарубежья, а самосвалы и прочее тем более не нужны Европе, все давно уже привыкли к комфортабельным, а самое главное - экологичным тягачам, "КАМАЗу" для этого пока далеко - поэтому основной его рынок сбыта - внутренний!
Сотников рассказал о том, как устроен гоночный грузовик «КАМАЗ-мастер» для «Дакара» — фото и видео
Вот уже почти четверть века российским грузовикам нет равных на ралли «Дакар» — самом жестоком марафоне планеты. Впервые команда «КАМАЗ-мастер» выиграла эту гонку в 1996 году и с тех пор стала доминирующей силой в своей дисциплине — за последние 18 лет лишь трижды соперникам удавалось превзойти «Синюю Армаду».
И что любопытно, челнинцы даже не скрывают своей техники и рассказывают о ней всем желающим — как, например, в недавнем выпуске YouTube-шоу «Путевые заметки», которое ежедневно выходит на канале «КАМАЗ-мастера». Лидер нынешнего «Дакара» Дмитрий Сотников показал свой грузовик и всё о нём рассказал.
«Вес «сухого» автомобиля без запчастей и топлива — 8 500 килограммов, это как раз соответствует правилам, которые применяются на «Дакаре», — начинает рассказ Сотников. — Двигатель мы используем 13-литровый, рядная «шёстёрка», дизельный двигатель — это тоже в соответствии с правилами. Больше 13 литров мы не имеем права использовать. Каждый год мы сами его потихонечку форсируем — это настоящий спортивный двигатель.
Двигатель грузовика Сотникова
Здесь вы видите два радиатора — так называемые интеркулеры. Воздух, который засасывается сверху крыши, после турбины охлаждается и только потом попадает в двигатель. Чем лучше охлаждён этот воздух, тем больше топлива можно сжечь и больше мощности получить.
Топливные баки, их три. Общая ёмкость — 900 литров. Задний — примерно на 200 литров, ещё два бака симметрично по краям — они примерно по 350. Такое расположение выбрано для улучшения центра масс — он получился ниже, а также для более правильного баланса по ходу гонки — идёт более равномерное распределение во время движения.
Центральный топливный бак
Самый большой расход топлива на сегодняшнем этапе был 170 литров — это как раз в секции дюн. А потом стал падать где-то до 110, но в среднем было 140. Это нормально, бывает и больше.
Передняя подвеска гоночного «КАМАЗа»
Мы используем по два амортизатора на колесо. Спереди мы ставим амортизаторы с пружиной, а сзади используем только рессору и просто амортизатор. Спереди тоже есть рессора, но подвеска настроена так, что мы используем дополнительную пружину — для более точной настройки жёсткости. Сзади достаточно только рессоры и амортизатора, но впереди нужны два упругих элемента.
Запасная турбина в кузове
Турбина. Здесь также видно кувалду, но не приходилось ей пользоваться — она уже на экстремальный ремонт. Здесь также стоит ящик и трапы сверху — в ящике лежит весь основной запас мелких запчастей, которые могут пригодиться. И сегодня также достали фал и привязали его сверху: дюны это всегда непредсказуемо, взаимопомощь на трассе в них — обычное дело.
С двигателя мощность вся передаётся на автоматическую коробку передач и уже от неё дальше — на раздаточную коробку, которая в центре, и от раздаточной коробки симметрично идёт распределение мощности перед/зад. Карданные валы соединены от раздаточной коробки с задним мостом и с передним.
Колесо гоночного «КАМАЗа»
Мы используем шины «Гудьир» на всех автомобилях. Одна из их особенностей конкретно этих шин — это размер диска 22,5 дюйма. Это диск большего размера, что помогает лучше вентилировать, особенно когда греются тормоза, и это помогает их охлаждению. К тому же лично мне они нравятся, потому что контроль автомобиля намного выше, чем у диска диаметром 20 дюймов.
Я предполагаю, что разгон до ста — в пределах восьми секунд. Это зависит от комплектации, массы грузовика и покрытия».
Увидеть рассказ Дмитрия Сотникова в сопровождении видео вы можете в выпуске «Путевых заметок» от 4 января 2021.
Китайский мотор, финские мосты: тест-драйв самого быстрого КамАЗ в мире
На первый взгляд, ничего особенного здесь нет, поскольку такая картина имеет место всякий раз, когда команда «КАМАЗ-мастер» выезжает на ралли «Дакар». Но если не смотреть это по телевизору, а оказаться в кабине этого гоночного грузовика, ощущения будут совершенно иные.
Команда и ее традиции. Команда «КАМАЗ-мастер» имеет отличную традицию – летом и осенью собирать представителей прессы с целью рассказать и показать, чем живет легендарный коллектив. Обязательной частью такой программы становится поездка на спортивном камине (так называют гоночный грузовой автомобиль), продолжительностью 20 минут на специальном полигоне для испытаний.
Но вначале стоит сказать несколько слов о самой команде. Это совсем не гараж небольшого размера, а отличная и огромная база, где выполняется постройка и ремонт автомобилей. Здесь самостоятельно делаются рамы, форсируются моторы, по причине чего штат сотрудников «сборной по автомобильному спорту» составляет порядка 200 человек.
Поэтому, наблюдая за моментами, когда команда из России будет громить очередного соперника на машинах иностранного производства, стоит иметь в виду, что это является результатом кропотливой и тщательной работы. Немалую роль в этом играют партнеры команды. За все основные моменты ответственность несет известная компания Total – в спортивные КАМАЗы залиты только масла и жидкости, рекомендованные специалистами этой компании после тщательного отбора.
Конструкция автомобилей. Устройство боевых машин заслуживает отдельного рассказа, так как ни для кого не секрет, что от серийных автомобилей там нет практически ничего. Это соответствует действительности, так как от товарной машины компания взяла для установки на гоночные только кабину. Но это является нормальным, так как конкуренты в большей части случаев поступают так же.
Поездка на автомобиле стала намного комфортнее после сделанных улучшений, но все же ощущения захватывают.
В этом и состоит искусство создания проектов для многотонных грузовых автомобилей спортивного назначения. Разрешается брать любые компоненты от любого производителя, но из них требуется собрать быстрый, легкий и надежный автомобиль. Следующим этапом будет настройка машины, а управлять ей будут опытные пилоты, штурманы, обслуживать опытные механики.
Теперь о составных частях: мосты поставляет финская Sisu, автоматические коробки — американская Allison, амортизаторы — голландская Reiger. Силовая установка же китайского производства – DCEC, несмотря на то, что немало людей ошибочно называют двигатели объемом 13 литров «Камминсом». В команду они приходят в стандартной комплектации, мощностью 400 л.с., где инженеры уже доводят мощность до 1000 л.с. Смазка выполняется правильно подобранным маслом, предоставляемым техническим партнером команды – компанией Total.
Поездка на автомобиле стала намного комфортнее после сделанных улучшений, но все же ощущения захватывают. До 100 км/ч машина разгоняется на грунтовой дороге за 10 секунд на «механике», с «автоматом» за 6 секунд. Для управления нужно не только отличное зрение, стальные мышцы и скорость от природы, но также и фантастическое умение чувствовать габариты.
Заключительной частью поездки стал фирменный трюк в виде разгона и прыжка с полуметрового трамплина, во время которого присутствует ощущение зависания в воздухе.
Заключение. Заключительной частью поездки стал фирменный трюк в виде разгона и прыжка с полуметрового трамплина, во время которого присутствует ощущение зависания в воздухе. После приземления, во время парковки пилотом машины, имеется возможность перевести дух.
Что в гоночном Камазе от Камаза?
«КАМАЗ-мастер» – самая успешная российская команда в автоспорте. Сегодня команду знают во всём мире, на её счету 14 побед в самом престижном ралли-рейде планеты, «Дакар». Фактически, именно «КАМАЗ-мастер» организует и вторую по значимости гонку в этой категории автоспорта – «Шёлковый путь», где, несмотря на жёсткую конкуренцию, доминирует почти безраздельно. Не стал исключением и «Шёлковый путь-2017», где грузовики КАМАЗ заняли три первых места грузового зачёта.
История команды началась почти 30 лет назад – официальной датой создания «КАМАЗ-мастер» считается 17 июля 1988 года. Конечно, тогда это была просто спортивная команда при заводе КАМАЗ, а в качестве техники использовались серийные грузовики, подготовленные для гонок при помощи только что созданного Научно-технического центра (НТЦ) компании. Там же поначалу команда и базировалась – лишь позже она получила собственное помещение по соседству.
Победы «КАМАЗ-мастер» прибавили бренду «КАМАЗ» узнаваемости по всему миру, но с годами команда всё дальше отходила от материнской компании как в конструкторском, так и в организационном плане. Менялись и сами грузовики. И сегодня в среде болельщиков всё чаще можно услышать вопрос: «А что в этой машине от КАМАЗа?»
Конечно, от чисто серийного КАМАЗа в машине мало что осталось. Сами посудите, эти автомобили предназначены совершенно для разных условий эксплуатации. Серийный КАМАЗ предназначен для транспортировки грузов из точки А в точку Б. Для него главное — эффективность, стоимость перевозок, стоимость самого автомобиля, стоимость владения, ремонтопригодности и так далее. У нас же гоночная машина. Ведь никто не додумается на Формулу 1 что-то ставить от серийного автомобиля, будь то Mercedes, Renault или Ferrari. Совершенно другие условия, совершенно другие требования. И, естественно, подход несколько другой.
Аналогичный подход используется всеми командами во всех сколь-нибудь значимых гоночных чемпионатах – никто не выставляет на старт серийные машины. Сегодня заводская команда отличается от частной не тем, что использует серийные шасси, а тем, что применяет свои ноу-хау, демонстрируя свои возможности. Таких ноу-хау у «КАМАЗ-мастер» предостаточно. Ведь в отличие от всех остальных гоночных команд с российским «паспортом», «КАМАЗ-мастер» действительно создаёт свои машины в России, силами своих специалистов. Других в команде попросту нет – зарубежных конструкторов в команду не приглашают.
«Самое главное – то, что мы строим грузовики сами, – поясняет Владимир Губа. – Самое главное, что у нас есть «камазовское» в наших автомобилях – это их конструкция, компоновка, грамотно подобранная композиция вот этих узлов агрегатов, которая в итоге дает возможность создать вполне конкурентоспособный грузовик, позволяющий на протяжении многих лет лидировать на внедорожных международных гонках, включая «Дакар». Это ноу-хау, которыми владеет команда, и которые позволяют из вроде бы известных элементов создать продукт с действительно выдающимися свойствами и качествами».
Нередко можно и слышать и о том, что «КАМАЗ-мастер» не может считаться чисто российской командой, потому что использует иностранные агрегаты – в частности, двигатели. Но в действительности часть побед КАМАЗов на «Дакарах» была одержана на отечественных двигателях – производства Ярославского (а ныне Тутаевского) моторного завода. Эти моторы использовались командой ещё совсем недавно, но сегодня на машинах их нет.
Виной тому, однако, вовсе не плохие характеристики двигателей, а регламент – тутаевские моторы были очень большого размера, 18,5 литров, тогда как регламент сегодня не позволяет ставить на грузовики силовые установки более 16 литров, а уже в следующем году их максимальный объём будет ограничен 13-ю литрами. В связи с этим конструкторам «КАМАЗ-мастер» пришлось искать им замену, и так как в России подходящих моторов не оказалось, они обратились к иностранным производителям. Однако подобная тактика – обычное дело для современных команд.
Сейчас, в эпоху глобализации, в эпоху тесного сотрудничества между фирмами, уже не стоит так вопрос: вот это наше, свое, отечественное, родное, и мы другого не хотим признавать. Сейчас иной подход: все стараются использовать самое лучшее, самое эффективное. То есть, фирма или конструктор стремится делать самостоятельно только то, что у него наилучшим образом получится. Если же что-то можно купить за меньшие деньги и эффективно использовать, то так и нужно поступать – так все и делают. Есть ряд фирм, которые специализируются на изготовлении узлов, деталей, компонентов, они очень долго этим занимаются, имеют соответствующую разработческую, исследовательскую, производственную базу. И, естественно, пытаться делать такие же детали или системы самому не имеет смысла.
Да, мы ставим на гоночные машины ряд иностранных компонентов. Но мы стараемся максимально использовать узлы и агрегаты тех фирм, которые сотрудничают с КАМАЗом. Те же двигатели, которые мы используем – мы не просто берём лучший в мире двигатель, а выбираем те моторы, которые имеют какое-то отношение к КАМАЗу. Сейчас на грузовиках стоят двигатели Liebherr, а эта компания – партнёр КАМАЗа, поставщик оборудования для моторного завода КАМАЗ. Сейчас идёт разработка нового двигателя с участием Liebherr.
Коробка передач на наших машинах – Zahnrad Fabrik. У нас в Набережных Челнах есть совместное производство «ZF-КАМА», которое выпускает коробки передач для грузовиков. И те коробки передач, что мы используем, тоже собираются здесь, в Челнах. Причём, на серийные грузовики КАМАЗ коробки ставятся аналогичные. Действительно аналогичные – просто мы используем более тяжёлые версии, а на серийных грузовиках устанавливаются более лёгкие. Рулевое управление – тоже Zahnrad Fabrik, и мы тоже используем их на серийных КАМАЗах.
Мосты мы ставим фирмы Sisu. Эти мосты лучше всего подходят к нашей конструкции, но среди команд используем их не только мы. Скажем, Iveco, хотя имеет собственную, мощную производственную базу, тоже использует финские мосты Sisu. Аналогичные мосты стоят на грузовиках большинства команд – с точки зрения массы, прочности, надежности они лучше подходят для тяжелых условий эксплуатации, ведь они созданы для военного применения.
Рамы мы делаем исключительно сами, на нашем производстве, начиная с профилей из специальной стали. Всё электрооборудование на автомобиле мы тоже сами разрабатываем, проектируем и устанавливаем. Электронные системы – блок управления двигателем, программное обеспечение – это тоже российская разработка, петербургской фирмы «Абит». Она тесно сотрудничает с КАМАЗом, поставляет на автомобили спец-исполнения, на спецтехнику, блоки управления. Эти блоки отличаются повышенной надежностью. Это российская разработка – не чисто камазовская, но российская».
Ещё важнее то, что подобный подход сегодня применяется далеко не только в автоспорте. Никто из современных автоконцернов не производит автомобили, будь то грузовые или легковые, целиком на своих заводах. В этом просто нет смысла – гораздо выгоднее покупать часть оборудования у компаний, которые на нём специализируются. А в случае необходимости поставщика всегда можно поменять.
«Даже в советский период КАМАЗ был сориентирован таким образом, что 60% агрегатов производится на заводе – кабина, двигатели, мосты, коробка передач – рассказывает главный конструктор КАМАЗа и директор НТЦ Данис Валеев. – Около 30% комплектующих мы покупали на российских предприятиях, и около 10% – за рубежом. Конечно, это были страны СЭВ – Югославия, Польша, ГДР…
Теперь соотношение собственных и закупаемых запчастей будет обратным – 40% мы производим, 60% будем закупать. Таким образом, глубина переработки на самом предприятии будет всё меньше и меньше. Но мы выделили ключевые области, в которых планируем сохранить собственное производство. Это кабины – и то, часть кабин будет собираться на совместном предприятии, – двигатели и мосты. Коробки будут закупаться, рамы тоже – будем работать с готовым профилем.
К таким мерам подталкивает экономика – иначе производство не окупается. Кроме того, появляется свобода выбор – мы можем договариваться с поставщиками из Китая, из Европы, из Индии и так далее. Разумеется, это не наша идея – в мире такой переход произошёл гораздо раньше. Все стараются выделить ключевые компетенции, которые определяют их конкурентоспособность, а остальное – закупать на стороне».
Меры эти отчасти вынужденные – в России попросту нет компаний, выпускающих продукцию достаточно высокого качества, и нет специалистов, способных такую продукцию спроектировать. Причём, это не проблема последних лет – такой ситуация была ещё в советское время.
«Проблема в том, что в конце 80-х и в 90-е годы у нас почти не развивались соответствующие технологические направления, – рассказывает Данис Валеев. – К примеру, у нас в стране не было сцеплений. С самого начала это было проблемой – мы использовали двухдисковое сцепление ненормального размера, и не имели соответствующих накладок. Можно было бы пойти по пути развития собственных разработок, как пробовал Тюменский моторостроительный завод, но у них ничего не получилось. Потому что всё упирается в инвестиции – на создание таких конструкций нужно было много денег.
После пожара на заводе двигателей в середине 90-х произошло переосмысление тех мощностей, что у нас есть. Тем более, что в конце 90-х – начале 2000-х у нас просто не было инвестиций, и не было возможности вкладывать деньги в закупку оборудования. Поэтому начали работать с внешними производителями – в том числе и зарубежными. Но речь не просто о покупке агрегатов – мы создаём совместные предприятия, это трансферт технологий. Мы создали СП с Cummins, ZF, Knorr-Bremse, Federal-Mogul…»
Теперь плодами сотрудничества завода с этими компаниями пользуется и команда. Но если львиную долю комплектующих производят специализированные фирмы, купить которые может любой желающий, то в чём заслуга «КАМАЗ-мастер» в её успехах? И почему челнинскую команду вот уже много лет никто не может победить – в том числе, используя аналогичные коробки передач и мосты?
«Конечно, не всё так просто – нельзя купить все необходимые детали и собрать хороший грузовик, – поясняет Данис Валеев. – И завод, и команда «КАМАЗ-мастер» работают по принципу формирования технического задания. Скажем, тот же 13-литровый двигатель разрабатывался по этому принципу, до этого они так же обращались к Buggyra, а создание автоматической коробки передач было поручено компании Allison. При этом, к примеру, основа двигателя – моторный блок, головка цилиндров – взяты в Китае, а заказы на создание поршневой группы уже размещаются в Европе. Таким образом, используется инновационный подход – двигатель производится за рубежом, но в соответствии с теми требованиями, что необходимы «КАМАЗ-мастер», и теми идеями, что есть у их конструкторов».
Успехи «КАМАЗ-мастер» настолько велики, что уже даже завод в каких-то случаях перенимает решения, разработанные для гонок, для своей техники – правда, не массовой, а специализированной. Хотя и тут процесс обмена опытом сталкивается с тем же препятствием – совершенно разными задачами производителя и гоночной команды.
«Да, какие-то вещи мы в своё время переняли у них – рассказывает Данис Валеев. – Не один к одному, конечно, но шли по тому же пути. Сейчас производство и разработки на КАМАЗе разделены на две части. Есть производство стандартных машин, старого и нового поколения, а есть создание специальной техники, в первую очередь военной. Много разработок на это направлены, и так как, из-за специфических условий эксплуатации, к таким машина предъявляются куда более жёсткие требования, и тут подобные решения применимы. К примеру, тяжёлый бронированный грузовой автомобиль, весом 20-22 тонны, имеет скорость на местности 60 км/ч, в то время как на серийной технике при такой массе – только 36 км/ч. Здесь есть решения, применяемые на гоночных грузовиках, которые мы стараемся воспроизвести. Кое-что подсмотрели по части сидений – не всё, конечно, потому что на военной технике сидения более сложные, взрывозащищённые. Но крепления, например, похожи. То есть, перенимаются не конструктивные решения, а опыт, который накапливает команда. Так что между нами действительно взаимовыгодный обмен информацией. Тем более, что когда-то мы вообще все работали на одной площадке».
Читайте также: